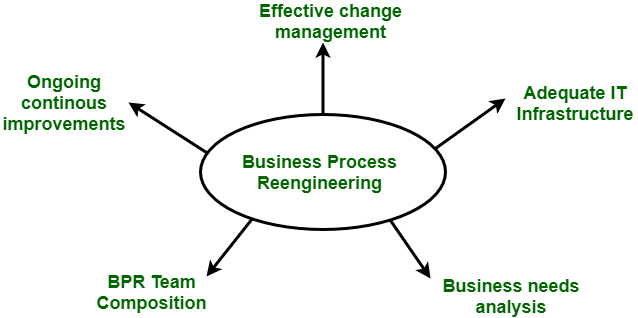
It is an essential part of an organization’s strategy. It can either make or break an organization's performance. Its success depends on how well crisis managers use the lessons from their experience to improve their practices. Crises managers must possess several psychological traits, such as task-oriented leadership behavior, communication plan, preparation. This article will discuss these attributes and how to prepare for a crisis. This article will make you more equipped to manage a crisis.
Crisis managers need to be able to recognize their psychological needs
Critical to their effectiveness, crisis managers must have strong psychological skills. These managers must be able think rationally, communicate effectively and avoid reacting in a panic situation. A key trait for crisis managers is empathy. Empathy is the ability of seeing the situation from the perspective of another person. They won't make the best informed decisions without empathy. They must be patient and not worry.
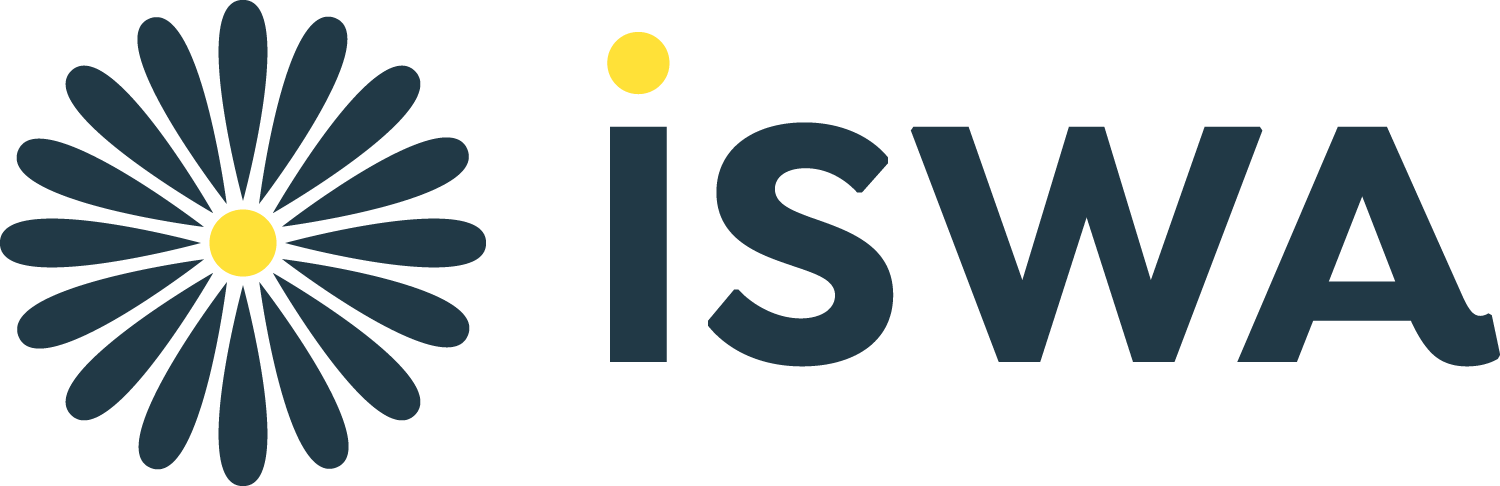
Leaders who are task-oriented
Although task-oriented leaders can be a good choice, there are dangers. Not only can task-oriented leadership be counterproductive, it can also create a hostile work environment. In this article we'll discuss some of the disadvantages of task-oriented leaders and how it can harm crisis managers. These are examples of situations where task-oriented leaders may be necessary.
Preparation to deal with crises
Although crises are inevitable, planning ahead can help you avoid them. Crises management experts recommend an in-depth assessment of any weaknesses or potential points of crisis. They also recommend pre-drafting crisis messages and conducting mock drills. It is important to practice crisis management skills before an actual crisis occurs. This will make it easier for crisis response personnel to make the best decisions. For more information, see Crisis in Organizations II (Code Red in the Boardroom)
Communication plan
A list of all contacts is an important step in developing a crisis communications plan. It is important to organize this information in a prioritized fashion so that customers who are most important can be reached first. It is important to outline in your plan how you will contact suppliers in case of emergency. This way you can communicate with suppliers whenever you need to and not rely on inefficient manual processes.
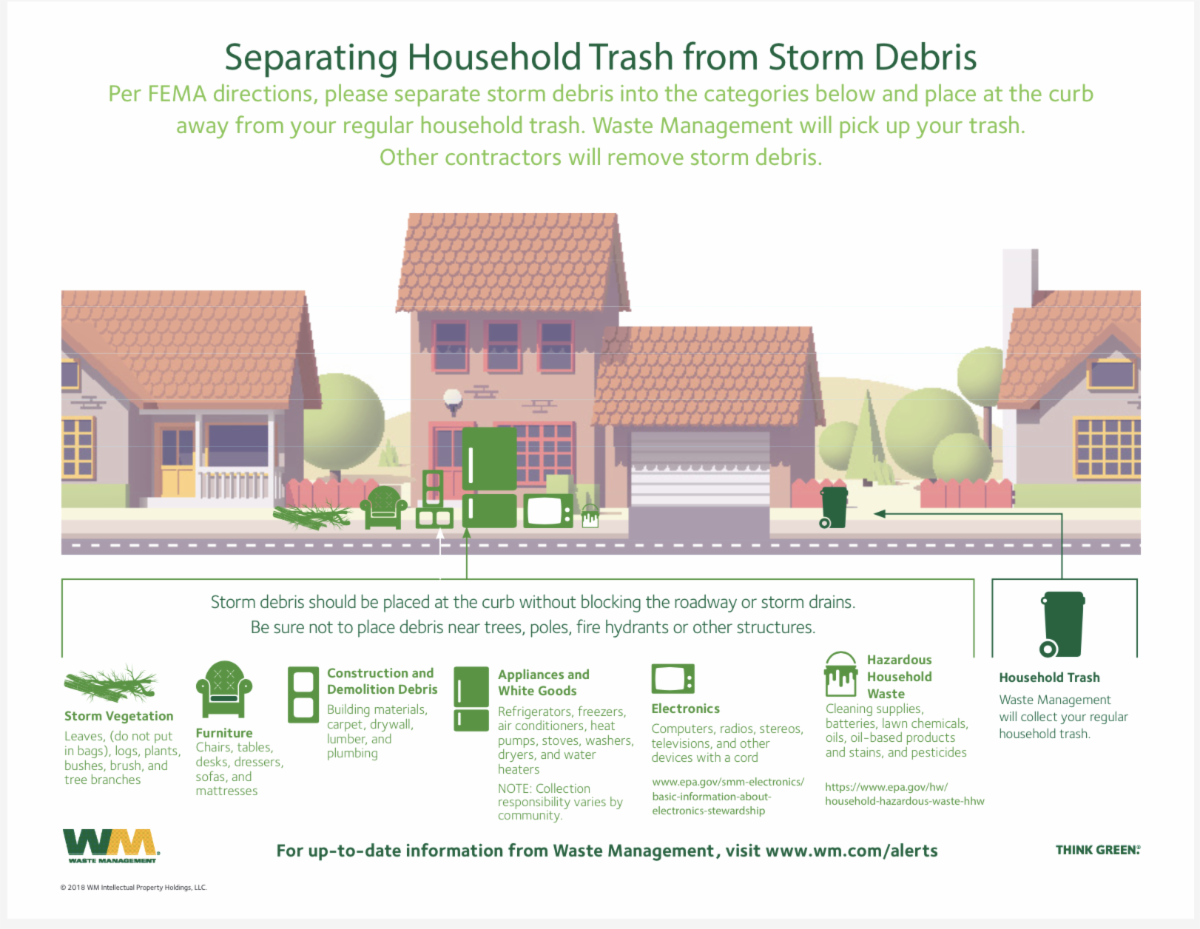
Public relations damage control
If you want to avoid PR disasters, it is important to learn how to manage them. Even though small businesses may lack the funds to hire a crisis manager, they can follow a specific protocol to deal with public relations issues. A proactive approach to dealing with issues will help avoid crises that can affect your reputation and business. A proactive approach to crisis managing is more cost-effective and efficient than waiting until controversy passes.
FAQ
How do you define Six Sigma?
Six Sigma will most likely be familiar to people who have worked in statistics and operations research. Anybody involved in any aspect or business can benefit.
It requires high levels of commitment and leadership skills to be successful.
Six Sigma is so popular.
Six Sigma can be implemented quickly and produce impressive results. It can also be used to help companies identify and focus on the most important aspects of their business.
What are the 3 main management styles?
The three basic management styles are: authoritarian, laissez-faire, and participative. Each style is unique and has its strengths as well as weaknesses. Which style do YOU prefer? Why?
Authoritarian - The leader sets the direction and expects everyone to comply with it. This style is best when the organization has a large and stable workforce.
Laissez-faire is a leader who allows everyone to make their own decisions. This style works best when the organization is small and dynamic.
Participative – The leader listens and takes in ideas from all. This style is most effective in smaller organizations, where everyone feels valued.
What is the difference in Six Sigma and TQM?
The main difference between these two quality management tools is that six sigma focuses on eliminating defects while total quality management (TQM) focuses on improving processes and reducing costs.
Six Sigma is a methodology for continuous improvement. It emphasizes the elimination of defects by using statistical methods such as control charts, p-charts, and Pareto analysis.
The goal of this method is to reduce variation in product output. This is done by identifying root causes and rectifying them.
Total quality management involves measuring and monitoring all aspects of the organization. It also includes training employees to improve performance.
It is often used as a strategy to increase productivity.
Statistics
- 100% of the courses are offered online, and no campus visits are required — a big time-saver for you. (online.uc.edu)
- UpCounsel accepts only the top 5 percent of lawyers on its site. (upcounsel.com)
- The profession is expected to grow 7% by 2028, a bit faster than the national average. (wgu.edu)
- Hire the top business lawyers and save up to 60% on legal fees (upcounsel.com)
- This field is expected to grow about 7% by 2028, a bit faster than the national average for job growth. (wgu.edu)
External Links
How To
What is Lean Manufacturing?
Lean Manufacturing methods are used to reduce waste through structured processes. They were developed by Toyota Motor Corporation in Japan during the 1980s. The primary goal was to make products with lower costs and maintain high quality. Lean manufacturing focuses on eliminating unnecessary steps and activities from the production process. It has five components: continuous improvement and pull systems; just-in time; continuous change; and kaizen (continuous innovation). It is a system that produces only the product the customer requests without additional work. Continuous improvement refers to continuously improving existing processes. Just-in-time refers to when components and materials are delivered directly to the point where they are needed. Kaizen is continuous improvement. This can be achieved by making small, incremental changes every day. The 5S acronym stands for sort in order, shine standardize and maintain. These five elements are used together to ensure the best possible results.
Lean Production System
Six key concepts make up the lean manufacturing system.
-
Flow - focuses on moving information and materials as close to customers as possible.
-
Value stream mapping is the ability to divide a process into smaller tasks, and then create a flowchart that shows the entire process.
-
Five S’s - Sorted, In Order. Shine. Standardize. And Sustain.
-
Kanban – visual signals like colored tape, stickers or other visual cues are used to keep track inventory.
-
Theory of constraints - identify bottlenecks during the process and eliminate them with lean tools like Kanban boards.
-
Just-in time - Get components and materials delivered right at the point of usage;
-
Continuous improvement: Make incremental improvements to the process instead of overhauling it completely.