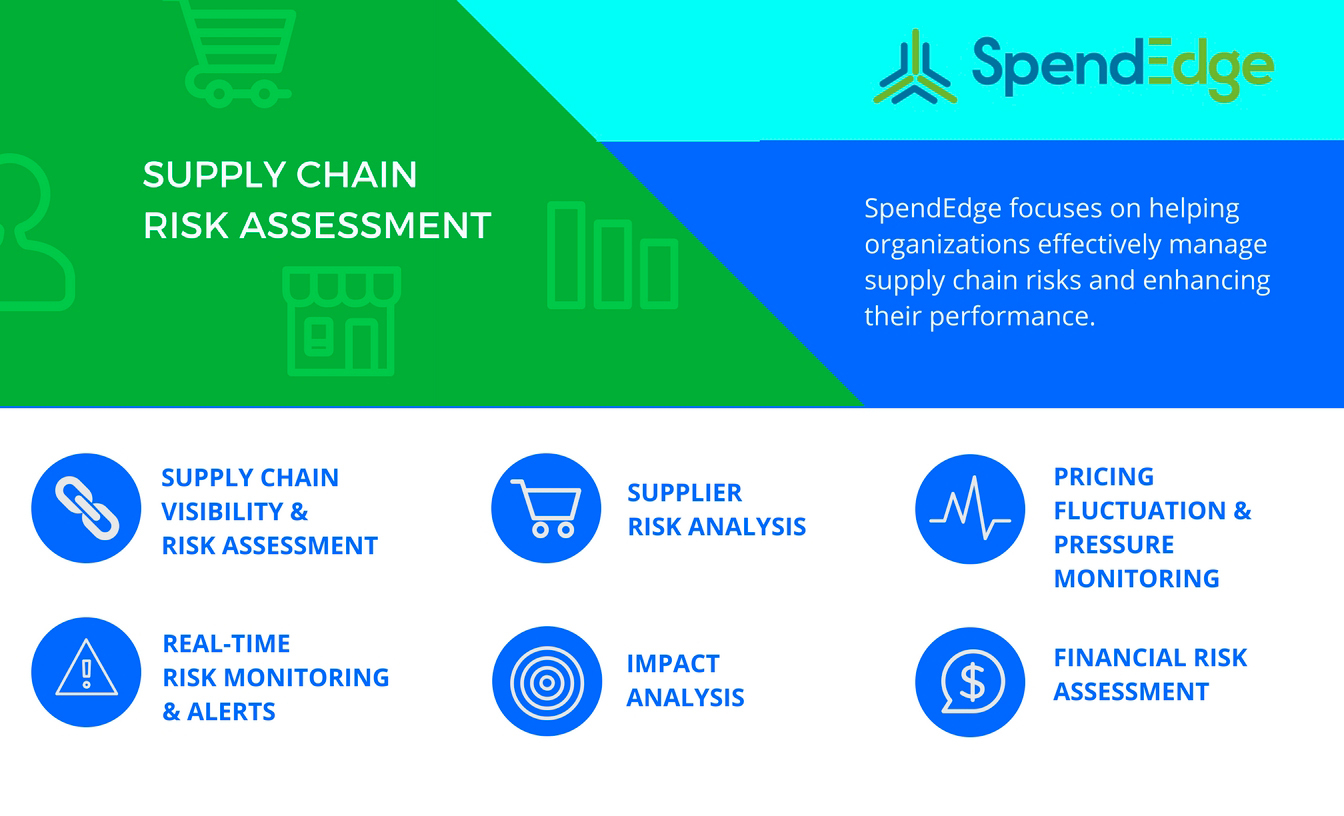
A safe management network is composed of a group of safes at a retail location. Each safe has a limited amount of control software. It is only possible to have well-defined functions in the terminal units' resident memory or processing capacity. Key control parameters are managed by a central servers. These servers can be a cluster of servers or a single cloud server. The safes are usually not connected to the Internet. This means that you don't need any external hardware.
Safe management system collects information
Safety management systems are a system that combines processes and procedures to reduce the risk of safety incidents. These systems can be highly effective but cannot eliminate all possible errors because they would not be practical, feasible, workable, or cost-effective. A safety management system cannot measure the behavior of every worker, so the information collected by it is not completely reliable. This information is nonetheless important in ensuring safety within the workplace.
Managers need to have access and an understanding of the data in order improve safety performance. This information can be used to improve safety performance using statistical techniques and other data sources. The data should be presented in an understandable manner. Moreover, the reports should be able to identify trends that can help managers allocate resources more effectively. These trends must be accommodated in safety management systems. The information should be easy to interpret and taken into consideration.
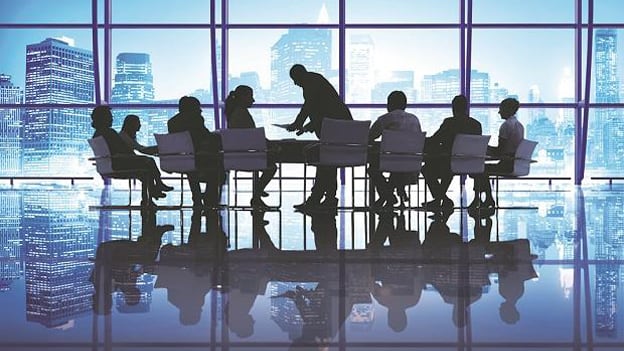
Documentation
The key ingredient to creating a safe management process is documentation. It prevents mistakes and helps you avoid re-learning old lessons. A management system should usually include processes for miscellaneous declarations, process safety, labeling and records retention. Documentation is essential for preventing injuries, accidents, or illnesses. Stakeholders have easy access to a complete document that outlines the best practices.
A good SMS documentation system will include all of the relevant international and national regulations, processes and procedures. It should also describe the outputs from the SMS and outline the structure and organization for the safety management system. Also, the documentation must include guidelines for maintaining records. To be effective safety documentation must be approved in writing by authorities. Additionally, safety documentation must reflect changes and be up to date.
Risk matrix
A risk matrix helps to manage organizational risks. A risk matrix allows you to prioritize risks according to their impact. The risk matrix uses categories such as Probability and Impact to help determine the risk level. Once you have determined the risks for your business, you can use the risk matrix to improve your existing risk control measures and reinforce your proactive safety culture. Here are some ways to create a Risk Matrix.
First, create a risk matrix. This document illustrates three types risk. Each level represents different risks. In Figure A1, the ground level represents the quantitative relationship between severity and probability. The middle floor represents linear scale, and the top floor is carpeted. Each column represents a different risk, which is represented by its corresponding numerical value. The formula RixCj is used to determine the risk indicator in each cell.
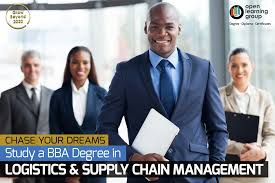
Safety assurance
In the process of developing a safety management system, it is important to define the requirements for a safety assurance procedure. Safety assurance procedures should cover all resources, reporting requirements, as well as disciplinary action. The procedure should also include a documented safety plan that is shared with all employees and regularly reviewed. The safety policy should include a list of the different levels within an organization that are able to make decisions regarding safety. The certificate holder should also indicate the types and levels of personnel and resources responsible for maintaining safety management.
The concept of safety assurance has developed in response to the growing exploitation of workers in industry. As the industrial revolution brought substantial commercial opportunities to Western societies, the financial imperative of business owners led to the use of an under-skilled workforce, including child labour, and rural migrant workers. These circumstances made it easy for accidents, injury, or even death to occur. Fortunately, safety management emerged as a counterweight to the exploitation of labour.
FAQ
Why is project management so important?
To ensure projects run smoothly and meet deadlines, project management techniques are employed.
This is because many businesses depend heavily upon project work to produce products and services.
These projects must be managed efficiently and effectively by companies.
Companies could lose their time, reputation, and money without effective project management.
What does Six Sigma mean?
Six Sigma employs statistical analysis to identify problems, measure them and analyze root causes. Six Sigma also uses experience to correct problems.
The first step is identifying the problem.
Next, data are collected and analyzed in order to identify patterns and trends.
The problem can then be fixed by taking corrective measures.
Finally, data will be reanalyzed to determine if there is an issue.
This cycle continues until the problem is solved.
What is Six Sigma and how can it help you?
It's an approach to quality improvement that emphasizes customer service and continuous learning. This is an approach to quality improvement that uses statistical techniques to eliminate defects.
Motorola invented Six Sigma in 1986 as part its efforts to improve manufacturing.
It was quickly adopted by the industry and many companies are now using six-sigma to improve product design, production, delivery, customer service, and product design.
How to manage employees effectively?
Effectively managing employees means making sure they are productive and happy.
This also involves setting clear expectations and monitoring their performance.
To do this successfully, managers need to set clear goals for themselves and for their teams.
They need to communicate clearly and openly with staff members. They need to communicate clearly with their staff.
They also need to keep records of their team's activities. These include:
-
What did you accomplish?
-
What was the work involved?
-
Who did it all?
-
What was the moment it was completed?
-
Why?
This information is useful for monitoring performance and evaluating the results.
What is the difference between leadership and management?
Leadership is about influence. Management is about controlling others.
A leader inspires others while a manager directs them.
Leaders inspire people to achieve success. Managers keep their workers focused.
A leader develops people; a manager manages people.
Statistics
- Your choice in Step 5 may very likely be the same or similar to the alternative you placed at the top of your list at the end of Step 4. (umassd.edu)
- The average salary for financial advisors in 2021 is around $60,000 per year, with the top 10% of the profession making more than $111,000 per year. (wgu.edu)
- UpCounsel accepts only the top 5 percent of lawyers on its site. (upcounsel.com)
- This field is expected to grow about 7% by 2028, a bit faster than the national average for job growth. (wgu.edu)
- The BLS says that financial services jobs like banking are expected to grow 4% by 2030, about as fast as the national average. (wgu.edu)
External Links
How To
How do you do the Kaizen method?
Kaizen means continuous improvement. This term was first used by Toyota Motor Corporation in the 1950s. It refers to the Japanese philosophy that emphasizes continuous improvement through small incremental changes. This is a collaborative process in which people work together to improve their processes continually.
Kaizen is one of the most effective methods used in Lean Manufacturing. In this concept, employees who are responsible for the production line must identify problems that exist during the manufacturing process and try to solve them before they become big issues. This is how you can improve the quality and lower the cost.
Kaizen is an approach to making every worker aware and alert to what is happening around them. So that there is no problem, you should immediately correct it if something goes wrong. So, if someone notices a problem while working, he/she should report it to his/her manager.
Kaizen is based on a few principles. We always start from the end product and move toward the beginning. In order to improve our factory's production, we must first fix the machines producing the final product. Next, we repair the machines that make components. Then, the machines that make raw materials. Then, we fix those who work directly with the machines.
This method is known as kaizen because it focuses upon improving every aspect of the process step by step. When we are done fixing the whole factory, we go back to the beginning and continue until we reach perfection.
How to measure kaizen's effectiveness in your business is essential to implement it. There are many ways you can determine if kaizen has been implemented well. Another method is to see how many defects are found on the products. Another way is to check how much productivity has grown since kaizen was implemented.
To determine if kaizen is effective, you should ask yourself why you chose to implement kaizen. Was it just because it was the law or because you wanted to save money? Did you really believe that it would be a success factor?
Let's say you answered yes or all of these questions. Congratulations! You're ready to start kaizen.