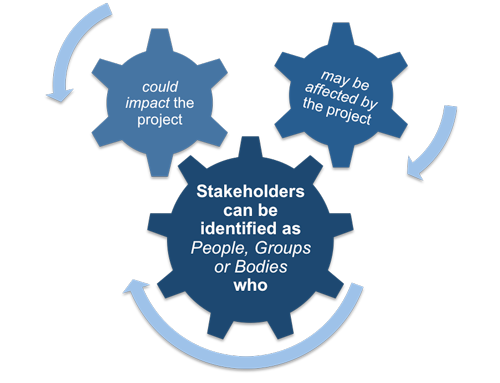
A company must adhere to 14 elements in order to be considered a PSM Program. These elements are Process hazard analysis, Permissible exposure limits and Physical data. These elements are crucial to the success of a PSM Program. By ensuring that the company follows these elements, a PSM program will be deemed compliant. These elements are described and illustrated in the following sections.
Analyses of Process Hazards
An essential element of any safety management program is the process hazard analysis. It helps to identify possible hazards and determine the consequences of failure. This analysis must be done by a team of employees who are knowledgeable about the process. It will examine the facilities' location and other factors such as past incidents. Once completed, the analysis needs to be updated every five-years. Hazard analysis must be used as part of safety management systems.
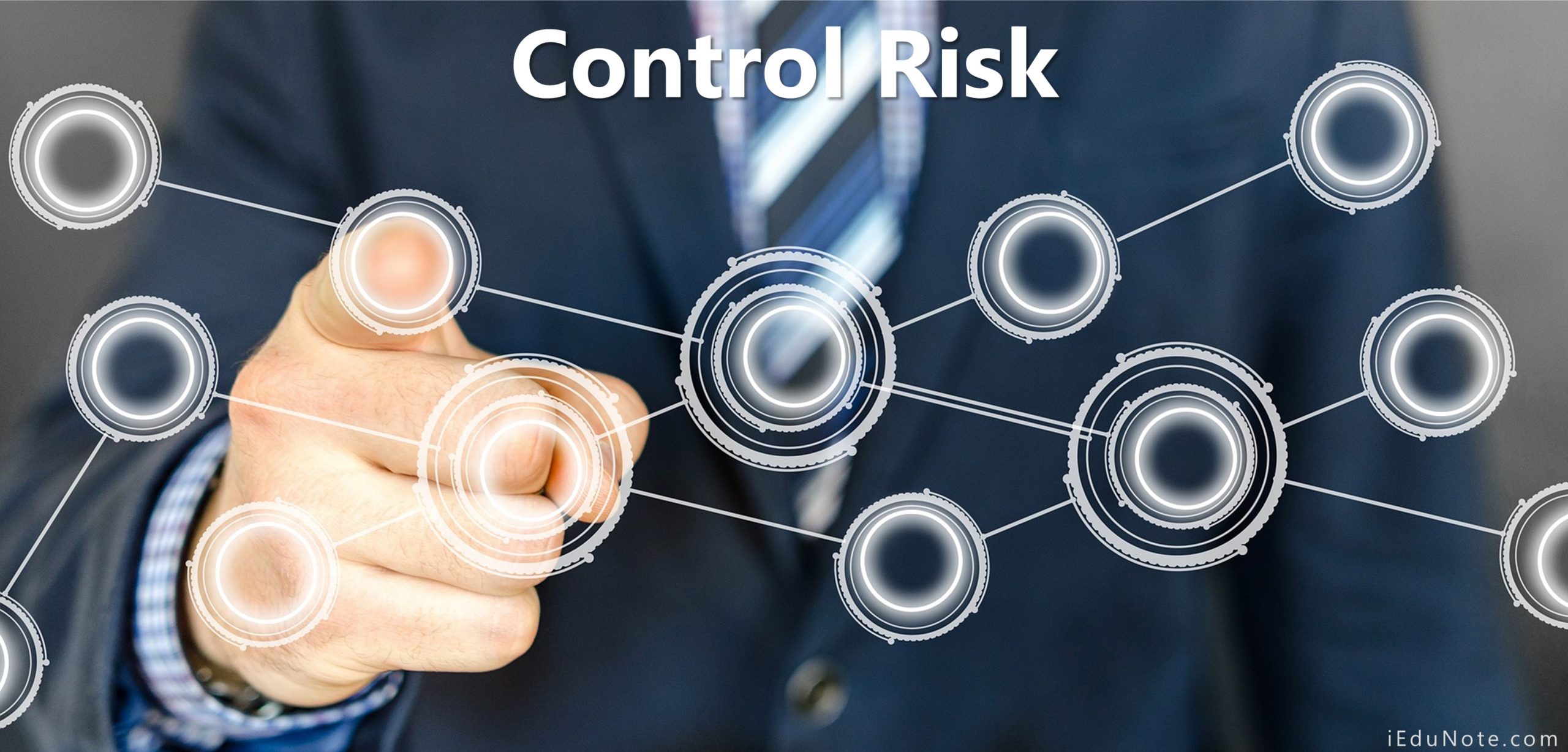
Permissible exposure limits
The OSHA Process Safety Management standard is a set of standards for processes that involve chemicals, gases, or liquids that are classified as hazardous. This standard is applicable to businesses that make or process hazardous chemicals. It does not cover hydrocarbon fuels used exclusively for workplace use, retail or well drilling. It also does not apply for facilities that are usually unoccupied or far away.
Physical data
PSM involves the assessment and management of hazardous products and materials. This entails understanding how to safely handle, transport, and store hazardous substances. This can lead to less product waste and fewer workplace accidents. It facilitates decision-making and helps organizations prioritize safety and health. PSM is an essential part of a safe workplace. It can help companies prevent costly medical emergencies and save money.
Corrosivity data
The PSM standard sets out requirements for how chemicals and other substances should be stored and handled. The PSM also contains requirements for emergency action plans, permit systems, as well as periodic compliance audits. No matter if your company uses hazardous substances in its production process, a PSM-compliant workplace can provide a safe environment that prevents accidents and damages.
Thermal stability data
OSHA has developed a standard for collecting and reporting PSM thermal stability data. Researchers will be more aware of possible hazards and less likely to accidentally release. It will be reviewed frequently and revised to address the tasks of new research projects. It will become accessible to all employees. The PSM includes information on toxicity (reactivity), corrosivity and physical properties.
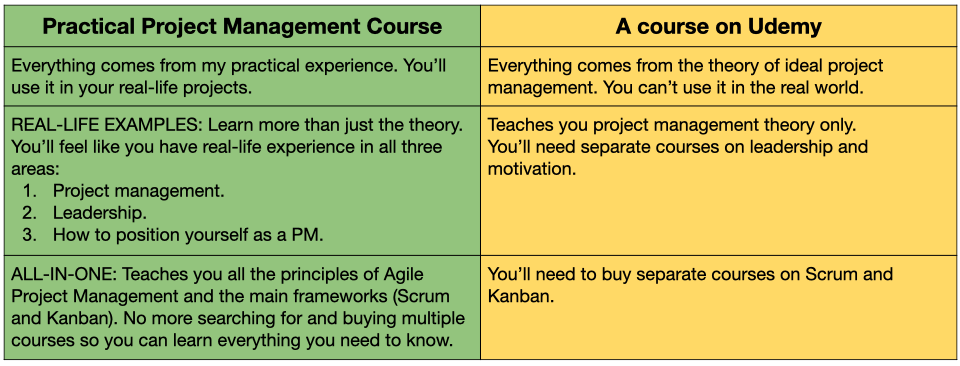
Employee participation clause
Process Safety Management (PSM), is a systematic and analytical approach to preventing process accidents due to highly hazardous chemicals (HHC). It is an important step in improving process safety and must be implemented at all levels, including maintenance and production. It contains 14 components that should be implemented. These include employee participation clauses. Here are some examples of elements and requirements.
FAQ
What are the steps of the management decision-making process?
Managers are faced with complex and multifaceted decisions. This involves many factors including analysis, strategy and planning, implementation, measurement and evaluation, feedback, feedback, and others.
Remember that people are humans just like you, and will make mistakes. This is the key to managing them. You are always capable of improving yourself, and there's always room for improvement.
This video will explain how decision-making works in Management. We'll discuss the different types and reasons they are important. Managers should also know how to navigate them. These topics are covered in this course:
What is the difference in a project and program?
A program is permanent, whereas a project is temporary.
A project usually has a specific goal and deadline.
It is often carried out by a team of people who report back to someone else.
A program typically has a set goal and objective.
It is typically done by one person.
What are the 3 basic management styles?
There are three types of management: participative, laissez faire, and authoritarian. Each style has its strengths and weaknesses. Which style do YOU prefer? Why?
Autoritarian – The leader sets the direction for everyone and expects them to follow. This style is most effective when an organization is large, stable, and well-run.
Laissez-faire is a leader who allows everyone to make their own decisions. This style works best when the organization is small and dynamic.
Participative - The leader listens to ideas and suggestions from everyone. This style works best in smaller organizations where everyone feels valued.
Statistics
- Hire the top business lawyers and save up to 60% on legal fees (upcounsel.com)
- 100% of the courses are offered online, and no campus visits are required — a big time-saver for you. (online.uc.edu)
- The average salary for financial advisors in 2021 is around $60,000 per year, with the top 10% of the profession making more than $111,000 per year. (wgu.edu)
- This field is expected to grow about 7% by 2028, a bit faster than the national average for job growth. (wgu.edu)
- Your choice in Step 5 may very likely be the same or similar to the alternative you placed at the top of your list at the end of Step 4. (umassd.edu)
External Links
How To
What are the 5S for the workplace?
Your first step in making your workplace more efficient and productive is to organize everything. A neat desk, tidy space, and well-organized workspace are key to productivity. The five "S"'s (Sort. Shine. Clean. Separate. And Store) help to maximize space and ensure efficiency. This session will go over each of these steps and show how they can be used in any setting.
-
Sort. Clear away clutter and paper so that you don’t spend time looking for it. This means you place items where you will use them the most. You should keep it close to the area where you research or look up information. It is important to consider whether or not you actually need something. If it does not serve a purpose, get rid of it.
-
Shine. Do not keep anything that could possibly cause damage or injury to others. For example, if you have a lot of pens lying around, find a way to store them safely. It might mean investing in a pen holder, which is a great investment because you won't lose pens anymore.
-
Sweep. To prevent dirt buildup on furniture and other items, clean them regularly. You may want to invest in some dusting equipment to ensure that all surfaces are as clean as possible. You can even set aside a specific area for sweeping and dusting to keep your workstation looking tidy.
-
Separate. Separating your trash into different bins will save you time when you need to dispose of it. To make it easier to throw away your trash without having to look for it, trash cans are often strategically placed throughout an office. Place trash bags next to each trash can to take advantage of the location.