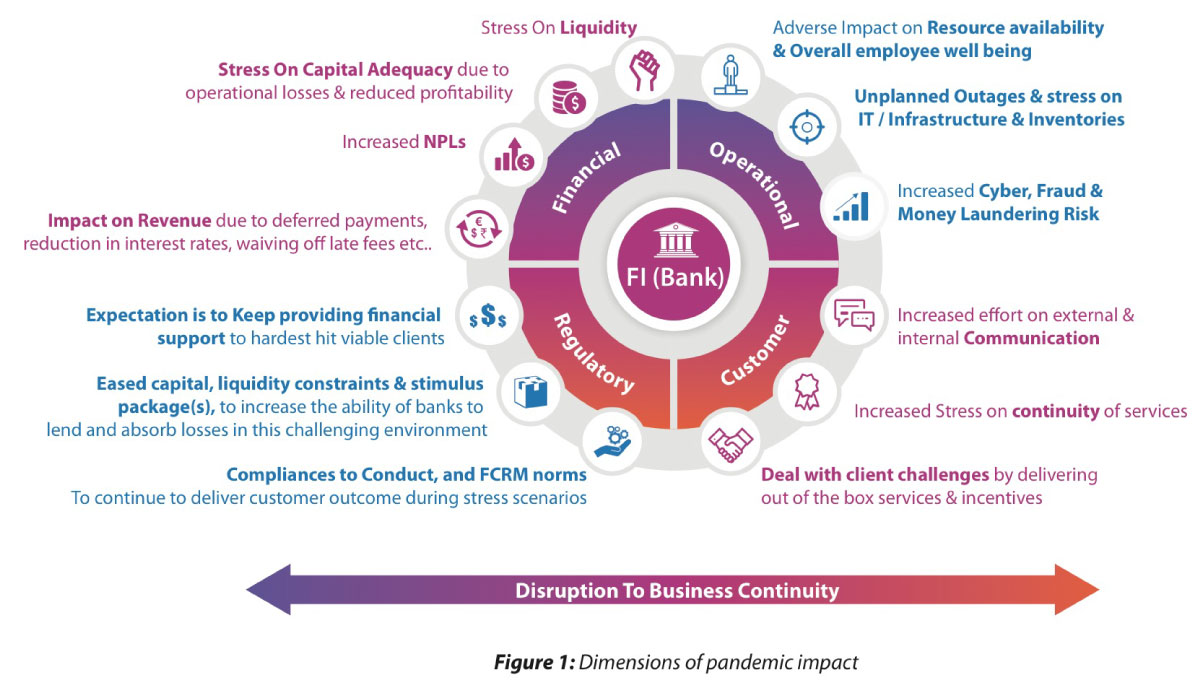
It is crucial to have waste removed from contaminated sites. The removal of hazardous materials and other contaminants from contaminated sites can help protect communities and the environment. No matter whether the problem occurs in urban, rural, and industrial areas, waste remediation may be an important step. You can read on to learn about the process and cost of waste remediation.
Methods of waste removal
It involves the treatment and disposal of hazardous substances. Incineration is one of the most common methods for treating hazardous materials. This involves heating or using electricity to heat solid waste. This reduces waste volume, transport costs, and harmful greenhouse gas emissions. Gasification is another method that uses low temperatures to extract energy, but without causing air pollution.
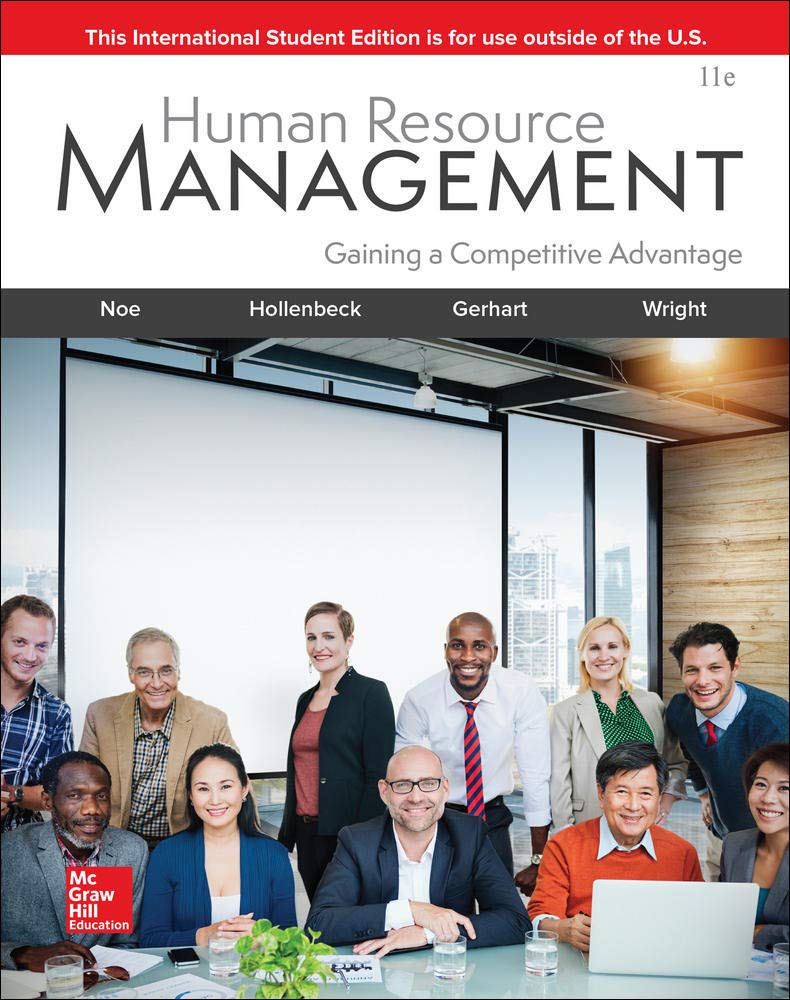
As the world population continues to grow, the need for an efficient way to dispose of waste has risen. Some areas, like those in developing countries are covered with a thin layer garbage before being filled with soil. After proper treatment, an area can be redeveloped into parkland and playgrounds.
Another method used in waste remediation involves the use of chemical disinfectants. While this process is best suited for liquid waste, it is also sometimes used for solid waste. There are many factors to consider when choosing the right chemical disinfectant for your particular waste. These factors include the type and concentration of the disinfectant, as well as the contamination. Also important is the amount of time that the waste has been in contact with.
Alternatives for RCRA's requirements to manage remediation waste
While alternatives to RCRA's requirements have been used for years for the management of remediation waste, their implementation has sometimes been problematic due to technical or legal issues. The EPA has created a new rule that will allow remediation projects the ability to use modified RCRA permits to simplify the requirements. These modified versions can be tailored to meet the specific needs of the facility, and the EPA is hoping that this will help improve cleanup procedures and safety.
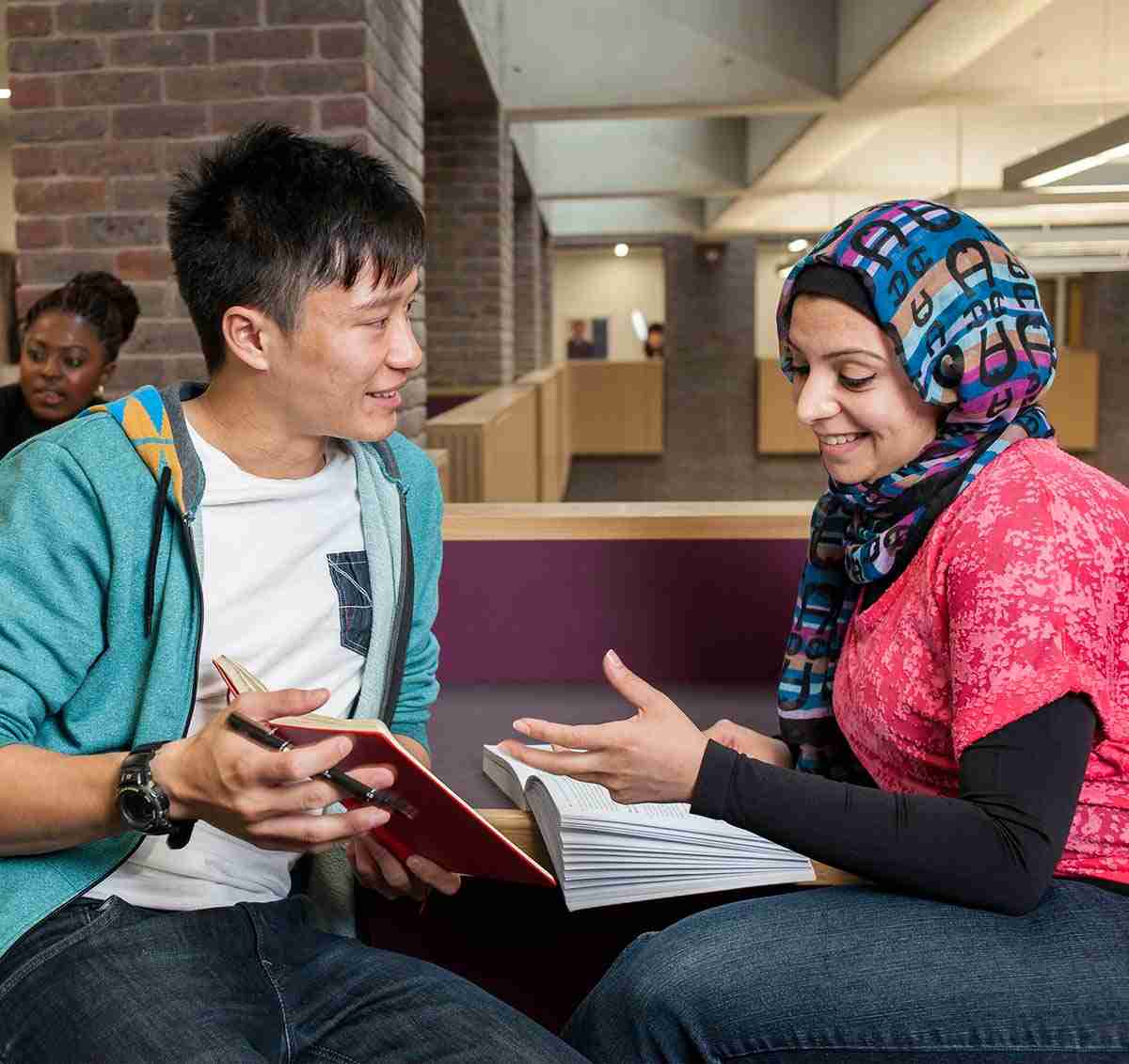
There are many alternatives to RCRA's requirements in remediation waste management. They can be used on-site as well as for removal. The former allows for the placement of remediation waste in containers or tanks or is treated ex-situ or removed from the AOC.
FAQ
What are some of the common mistakes made by managers?
Sometimes managers make their job harder than they need to.
They may not be able to delegate enough responsibility to staff or provide adequate support.
Many managers lack the communication skills to motivate and lead their employees.
Some managers create unrealistic expectations for their teams.
Managers may prefer to solve every problem for themselves than to delegate responsibility.
Six Sigma is so beloved.
Six Sigma is simple to implement and can yield significant results. Six Sigma provides a framework to measure improvements and allows companies to focus on the most important things.
Why is it important for companies to use project management techniques?
To ensure projects run smoothly and meet deadlines, project management techniques are employed.
This is because many businesses depend heavily upon project work to produce products and services.
These projects are essential for companies.
Companies can lose time, money, and reputation if they don't have a good project management system.
What is Six Sigma?
It's a strategy for quality improvement that emphasizes customer care and continuous learning. The goal is to eliminate defects by using statistical techniques.
Motorola invented Six Sigma in 1986 as part its efforts to improve manufacturing.
The idea quickly spread in the industry. Many organizations today use six-sigma methods to improve product design and production, delivery and customer service.
Statistics
- Your choice in Step 5 may very likely be the same or similar to the alternative you placed at the top of your list at the end of Step 4. (umassd.edu)
- As of 2020, personal bankers or tellers make an average of $32,620 per year, according to the BLS. (wgu.edu)
- UpCounsel accepts only the top 5 percent of lawyers on its site. (upcounsel.com)
- The average salary for financial advisors in 2021 is around $60,000 per year, with the top 10% of the profession making more than $111,000 per year. (wgu.edu)
- The profession is expected to grow 7% by 2028, a bit faster than the national average. (wgu.edu)
External Links
How To
How can you use the Kaizen method?
Kaizen means continuous improvement. This Japanese term refers to the Japanese philosophy of continuous improvement that emphasizes incremental improvements and constant improvement. It is a process where people come together to improve their processes.
Kaizen is one the most important methods of Lean Manufacturing. This concept requires employees to identify and solve problems during manufacturing before they become major issues. This is how you can improve the quality and lower the cost.
The main idea behind kaizen is to make every worker aware of what happens around him/her. It is important to correct any problems immediately if they are discovered. It is important that employees report any problems they see while on the job to their managers.
Kaizen is based on a few principles. Start with the end product, and then move to the beginning. In order to improve our factory's production, we must first fix the machines producing the final product. Next, we fix the machines which produce components. Then we fix the workers, who directly work with these machines.
This is known as "kaizen", because it emphasizes improving each step. Once we have finished fixing the factory, we return to the beginning and work until perfection.
To implement kaizen in your business, you need to find out how to measure its effectiveness. There are several ways that you can tell if your kaizen system is working. Another method is to see how many defects are found on the products. Another way is determining how much productivity increased after implementing kaizen.
If you want to find out if your kaizen is actually working, ask yourself why. It was because of the law, or simply because you wanted to save some money. Did you really believe it would lead to success?
Let's say you answered yes or all of these questions. Congratulations! You are ready to start kaizen.