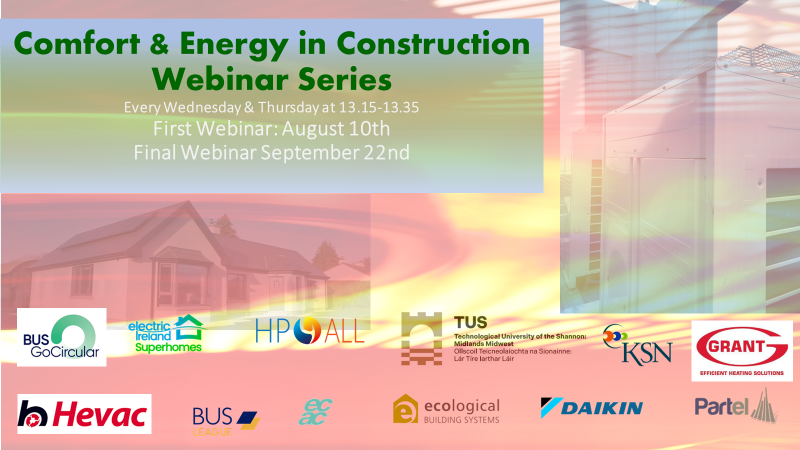
An essential part of project management is the identification and tracking of issues. It allows you to keep track everything that's happening and keeps everyone updated on how the project is progressing. You can keep track of issues using a log, a spreadsheet or another tool.
A variety of factors can create problems such as staff shortages or technical failures. They can be high priority or low priority and can impact a project's success. If ignored, they can cause major problems. You can track these issues using issue management techniques and make sure they are addressed.
Management of issues requires a plan and a strategy. You may choose to take multiple courses of action at once. To keep everyone informed about the status of issues, you might create an issue tracking dashboard. It is important to not confuse issues with risks. It is important to distinguish between them.
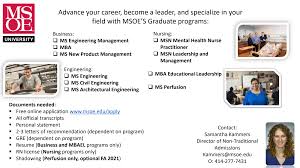
You can find issues at any level within an organization. If a team member is not skilled, it may be necessary to find an alternate resource. You may have to overcome issues in order to move on or accomplish the objectives of a project. A project can get stalled if an issue isn't addressed. Problem management can help you to identify and fix the issue, while minimising disruptions to the project.
It is possible to identify issues at all levels. But you must ensure that the information is made available to those who need it. This includes both those who must report on the issue as well as others who may be interested in how it impacts the project. It is possible to use a simple spreadsheet for tracking issues on projects that don't require as much detail as other projects.
It is important to recognize problems before you can prevent them. Sometimes, it is easy to identify problems by looking at the smallest details. For example, you might find out that a certain staff member is currently in hospital for two weeks. Follow up with your issue log if you identify an issue. You can also use it as an archival tool for later use.
You can also find opportunities in the face of problems. For instance, if a team member has a medical emergency, you may have an opportunity to hire an alternative team member. Sometimes, the problem can be solved by someone else. It can help you spot potential issues before they become major problems.
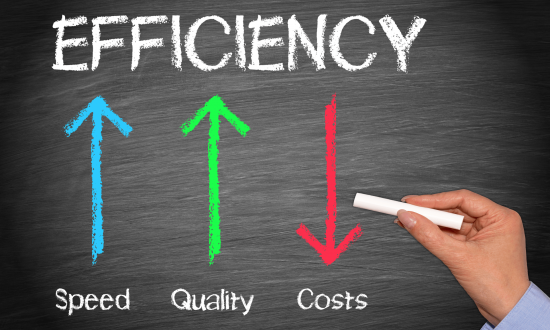
You can also refer to issue management as information technology service management, project management, or even information technology issue management. No matter what the name may be, project success is dependent on issue management. It involves identifying and tracking issues, assessing the impact of these issues, and implementing a plan to resolve them. It is essential to ensure that the process is connected to project governance.
Issues can be tracked in an issue log, a spreadsheet, or a project management tool of your choice. In general, keep your issue log updated with status updates, resolution comments, action items, and other information. Assign people to the issues as soon as possible, if this is possible. A detailed plan should be included in the log.
FAQ
What is Six Sigma?
Six Sigma employs statistical analysis to identify problems, measure them and analyze root causes. Six Sigma also uses experience to correct problems.
First, identify the problem.
Next, data will be collected and analyzed to determine trends and patterns.
The problem is then rectified.
Finally, data is reanalyzed to determine whether the problem has been eliminated.
This continues until the problem has been solved.
What kind of people use Six Sigma
Six sigma is a common concept for people who have worked in statistics or operations research. Anybody involved in any aspect or business can benefit.
It is a commitment-intensive task that requires strong leadership skills.
How does a manager develop his/her management skills?
By practicing good management skills at all times.
Managers must continuously monitor the performance levels of their subordinates.
You must act quickly if you notice that your subordinate isn’t performing to their standards.
You should be able to identify what needs improvement and how to improve things.
What is the difference of a program and project?
A project is temporary, while a program lasts forever.
A project has usually a specified goal and a time limit.
It is often done in a team that reports to another.
A program usually has a set of goals and objectives.
It is typically done by one person.
What is a fundamental management tool for decision-making?
A decision matrix can be a simple, but effective tool to assist managers in making decisions. It allows them to consider all possible solutions.
A decision matrix is a way to organize alternatives into rows and columns. This makes it easy for you to see how each option affects other options.
We have four options in this example. They are represented by the boxes to the left of the matrix. Each box represents an option. The top row depicts the current status quo, while the bottom row represents what would happen if no action was taken.
The effect of selecting Option 1 is shown in the middle column. In this example, it would lead to an increase in sales of between $2 million and $3 million.
The following columns illustrate the impact of Options 2 and 3. These positive changes can increase sales by $1 million or $500,000. However, these also involve negative consequences. Option 2, for example, increases the cost by $100 000 while Option 3 decreases profits by $200 000.
Finally, the last column shows the results of choosing Option 4. This will result in sales falling by $1,000,000
A decision matrix has the advantage that you don’t have to remember where numbers belong. You can just glance at the cells and see immediately if one given choice is better.
The matrix already does all the work. Simply compare the numbers within the cells.
Here's a sample of how you might use decision matrixes in your business.
Decide whether you want to invest more in advertising. If you do this, you will be able to increase revenue by $5000 per month. You will still have to pay $10000 per month in additional expenses.
The net result of advertising investment can be calculated by looking at the cell below that reads "Advertising." It is 15 thousand. Advertising is worth much more than the investment cost.
Statistics
- The average salary for financial advisors in 2021 is around $60,000 per year, with the top 10% of the profession making more than $111,000 per year. (wgu.edu)
- Your choice in Step 5 may very likely be the same or similar to the alternative you placed at the top of your list at the end of Step 4. (umassd.edu)
- Hire the top business lawyers and save up to 60% on legal fees (upcounsel.com)
- 100% of the courses are offered online, and no campus visits are required — a big time-saver for you. (online.uc.edu)
- This field is expected to grow about 7% by 2028, a bit faster than the national average for job growth. (wgu.edu)
External Links
How To
How is Lean Manufacturing done?
Lean Manufacturing methods are used to reduce waste through structured processes. They were developed in Japan by Toyota Motor Corporation (in the 1980s). The aim was to produce better quality products at lower costs. Lean manufacturing emphasizes removing unnecessary steps from the production process. It consists of five basic elements: pull systems, continuous improvement, just-in-time, kaizen (continuous change), and 5S. The production of only what the customer needs without extra work is called pull systems. Continuous improvement involves constantly improving upon existing processes. Just-in-time is when components and other materials are delivered at their destination in a timely manner. Kaizen is continuous improvement. This can be achieved by making small, incremental changes every day. Fifth, the 5S stand for sort, set up in order to shine, standardize, maintain, and standardize. To achieve the best results, these five elements must be used together.
Lean Production System
Six key concepts make up the lean manufacturing system.
-
Flow: The goal is to move material and information as close as possible from customers.
-
Value stream mapping - break down each stage of a process into discrete tasks and create a flowchart of the entire process;
-
Five S's: Sort, Shine Standardize, Sustain, Set In Order, Shine and Shine
-
Kanban - use visual signals such as colored tape, stickers, or other visual cues to keep track of inventory;
-
Theory of constraints - identify bottlenecks during the process and eliminate them with lean tools like Kanban boards.
-
Just-intime - Order components and materials at your location right on the spot.
-
Continuous improvement: Make incremental improvements to the process instead of overhauling it completely.