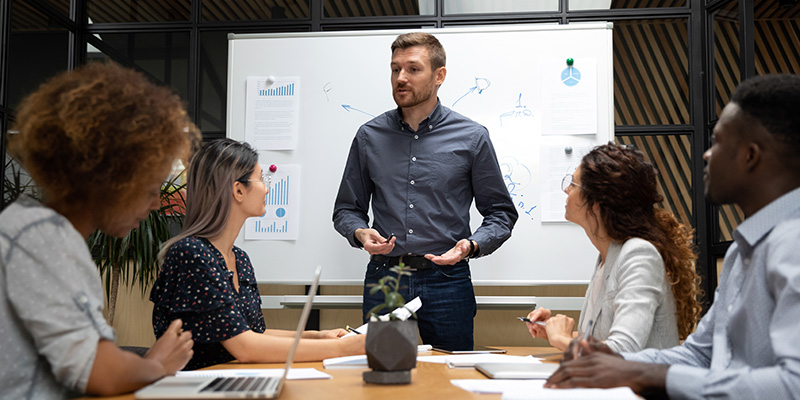
A supply chain decision making framework is a process that will help companies make decisions about different aspects of their business. Communication is a key component. The five steps that make up the rational process are: identifying the problem; analyzing potential solutions; gathering data; analyzing possible outcomes; deciding on the best solution.
Inventory is a key supply chain driver
Management of inventory is a key function of manufacturing firms. This allows the production of the right product at just the right time and place. This function becomes increasingly important in a global marketplace where products can easily be manufactured anywhere. It is crucial to a company’s efficiency as well as responsiveness.
Inventory management requires the ability to anticipate customer needs and respond to changing conditions. The data that companies share about their production schedules or inventory levels must be shared with their partners. This allows them to quickly react to market changes. In this highly dynamic world, inventory management is essential to ensuring that companies meet their customers' demands.
Communication and collaboration are key
Communication and collaboration are vital in today's fast-paced business world. These relationships allow companies to be more responsive to market changes and to differentiate themselves from their competitors. Collaboration can also be used to help organisations access new resources, learn new skills, and keep pace with their competitors. It can also be a way for businesses to grow their customer base.
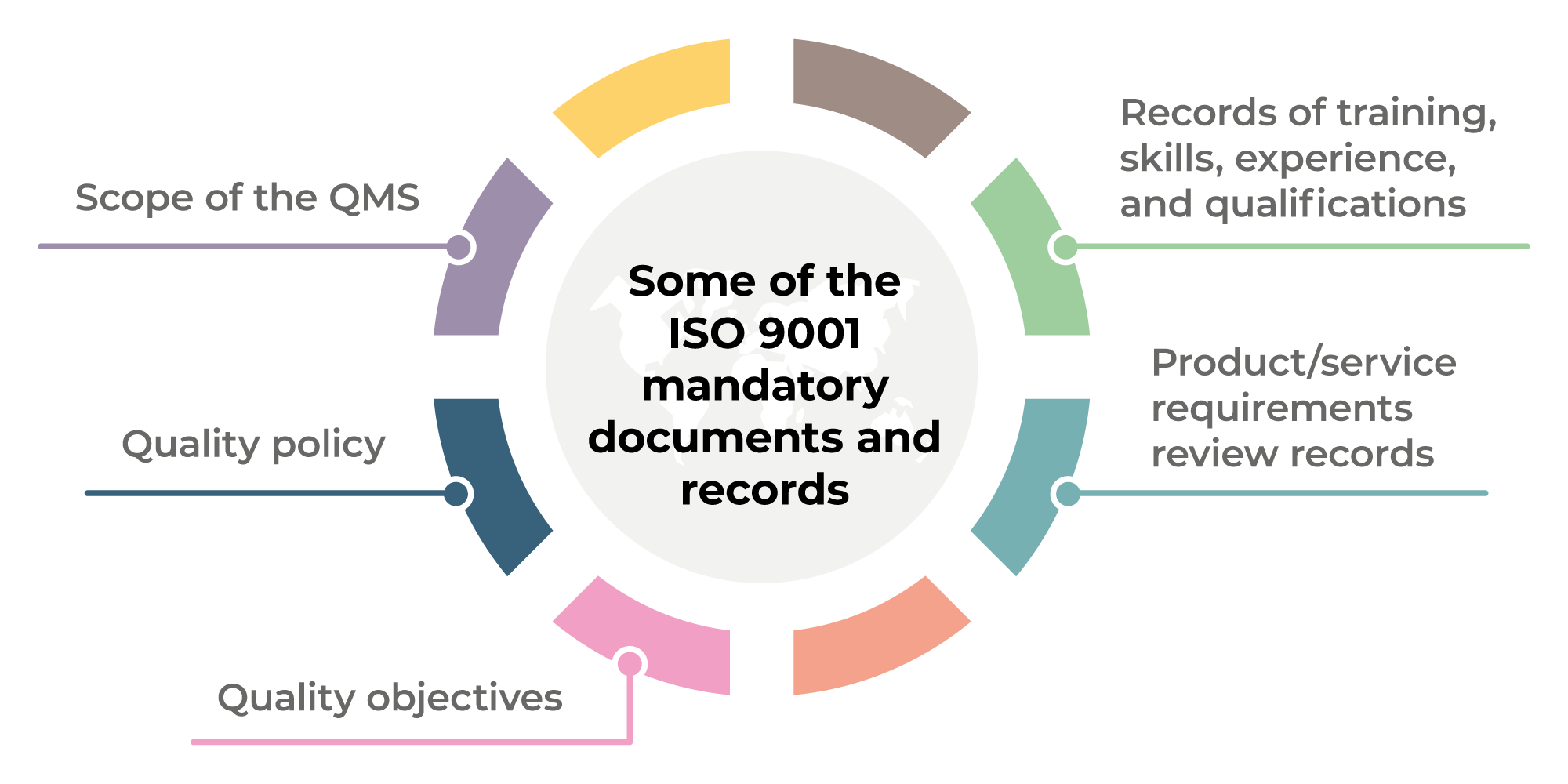
It takes trust and high commitment to create successful collaborative relationships. A culture that encourages collaboration is also essential.
Financial attributes
A framework for supply chain decision making must consider both financial and ecological factors. It is essential to improve the overall cash flow in the supply chain. These attributes will have an impact on the level of working capital at suppliers as well as buyers. This is important because the cash flow level is directly related to the level of finance leverage, access to capital, and financial stability of suppliers. SCF should be improved by financial attributes. Financial attributes also play a crucial role in investment in green technology and environmental policy. Financial and environmental policies directly link to social value.
This framework is a decision-making tool for supply chains and interlinks different components. It also addresses open research questions. The framework is useful across industries and sector.
Environmental attributes
The growing acceptance of environmental concerns is driving the trend to include environmental attributes in supply chain decision making. Many companies adopt environmental performance measures for a variety reasons. While environmental performance measurement may seem complicated, the benefits can be significant for both sides.
These attributes include social, financial and environmental criteria. This framework will help companies select the most eco-friendly suppliers to their businesses. It should also help them to adopt environmentally-friendly practices in their own businesses.
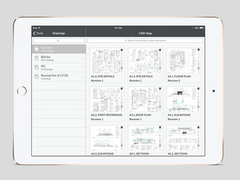
Prioritizing
Demand Prioritization is an important aspect of supply chain decision making. It is essential to identify the highest-profitable market and allocate resources accordingly. Sometimes, this may mean delaying orders or offering a substitute product. The process must be clearly documented and communicated to all levels to reduce risk. The supply side should provide input on costs, but the demand side should have the most information about customer desires and sales objectives.
Next, you need to find opportunities to acquire capacity, raw materials, or labor pools. An organization may be interested in exploring opportunities to purchase raw materials from other sources with lower prices and shorter lead times. However, it should also be noted that this can erode margin and working capital. Similar to the above, you may need to expand your operations during off-peak hours and to secure additional transport capacity.
FAQ
What are the five management methods?
Each business has five stages: planning, execution and monitoring.
Planning is about setting goals for your future. It involves setting goals and making plans.
Execution takes place when you actually implement the plans. You need to make sure they're followed by everyone involved.
Monitoring is checking on progress towards achieving your objectives. Regular reviews should be done of your performance against targets or budgets.
Each year, reviews are held at the end. They allow for an assessment of whether all went well throughout the year. If not, changes may be made to improve the performance next time around.
After the annual review, evaluation takes place. It helps to identify what went well and what didn’t. It also provides feedback on the performance of people.
What are some common mistakes managers make?
Managers can make their jobs more difficult than necessary.
They may not assign enough responsibilities to staff members and provide them with inadequate support.
Many managers lack the communication skills to motivate and lead their employees.
Some managers set unrealistic expectations for their staff.
Managers may choose to solve every problem all by themselves, instead of delegating to others.
What is Six Sigma and how can it help you?
It's an approach to quality improvement that emphasizes customer service and continuous learning. The objective is to eliminate all defects through statistical methods.
Motorola developed Six Sigma in 1986 to help improve its manufacturing processes.
This idea quickly spread throughout the industry. Today, many organizations use six sigma methods for product design, production and delivery.
Statistics
- The average salary for financial advisors in 2021 is around $60,000 per year, with the top 10% of the profession making more than $111,000 per year. (wgu.edu)
- Hire the top business lawyers and save up to 60% on legal fees (upcounsel.com)
- This field is expected to grow about 7% by 2028, a bit faster than the national average for job growth. (wgu.edu)
- UpCounsel accepts only the top 5 percent of lawyers on its site. (upcounsel.com)
- Our program is 100% engineered for your success. (online.uc.edu)
External Links
How To
How do you implement a Quality Management Plan (QMP)?
The Quality Management Plan (QMP) was established in ISO 9001. It is a systematic way to improve processes, products and services. It emphasizes on how to continuously measure, analyze, control, and improve processes, product/service, and customer satisfaction.
QMP stands for Quality Management Process. It is used to guarantee good business performance. The QMP aims to improve the process of production, service delivery, and customer relationship. QMPs must include all three elements - Products, Services, and Processes. If the QMP focuses on one aspect, it is called "Process." QMP. QMPs that focus on a Product/Service are known as "Product" QMPs. QMP stands for Customer Relationships.
When implementing a QMP, there are two main elements: Scope and Strategy. These elements can be defined as follows.
Scope: This describes the scope and duration for the QMP. This scope can be used to determine activities for the first six-months of implementation of a QMP in your company.
Strategy: This describes how you will achieve the goals in your scope.
A typical QMP has five phases: Planning (Design, Development), Implementation (Implementation), and Maintenance. Each phase is explained below:
Planning: In this stage, the objectives of the QMP are identified and prioritized. In order to fully understand and meet the needs of all stakeholders involved in this project, they are consulted. After identifying the objectives, priorities and stakeholder involvement, it's time to develop the strategy for achieving the goals.
Design: The design stage involves the development of vision, mission strategies, tactics, and strategies that will allow for successful implementation. These strategies can be implemented through the creation of detailed plans.
Development: Here, the team develops the resources and capabilities that will support the successful implementation.
Implementation: This refers to the actual implementation or the use of the strategies planned.
Maintenance: It is an ongoing process that maintains the QMP over time.
Several additional items should be added to the QMP.
Participation by Stakeholders is essential for the QMP's continued success. They need to be actively involved in the planning, design, development, implementation, and maintenance stages of the QMP.
Project Initiation: It is essential to have a clear understanding about the problem and the solution before you can initiate a project. Also, the initiator should understand why they are doing it and what they expect.
Time frame: It is crucial to know the time frame for the QMP. The simplest version can be used if the QMP is only being implemented for a short time. If you are looking for a longer-term commitment, however, you might need more complex versions.
Cost Estimation - Cost estimation is an important part of the QMP. Without knowing how much you will spend, planning is impossible. The QMP should be cost-estimated before it can begin.
QMPs are not just a written document. They should be a living document. It can change as the company grows or changes. So, it should be reviewed periodically to make sure that it still meets the needs of the organization.