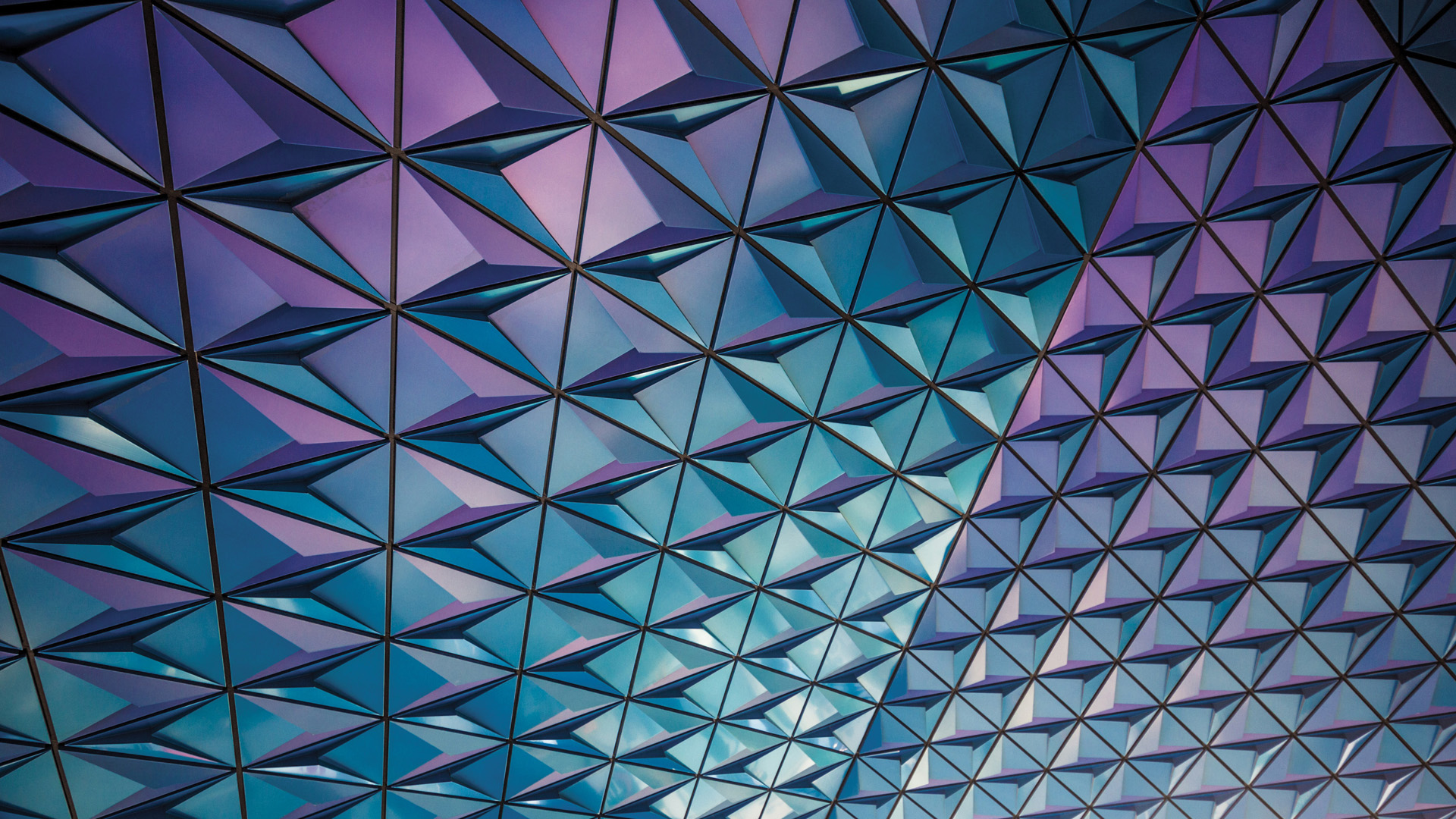
Definition of the role for middle management
In a company, the role of the middle manager is to link top-level management with lower level employees. They convert the executive team's strategy into departmental goals. In addition, they collect data and report results to the executive team. Their responsibilities extend from overseeing subordinates to making decisions about resource allocation.
Federal government middle managers are in similar or higher supervisory positions to front-line supervisors. This includes establishing guidelines and policies to govern the work done by lower-level employees.
Management of middle managers faces challenges
Many middle managers are faced with conflicting roles which can cause frustration. These managers have to manage subordinates as well as reporting to higher-ups. They also have to enforce policies, which may be contrary to their direct reports. Technology can help middle managers deal with this dilemma. For example, the PwC app identifies digital training opportunities and guides managers to over 300 courses.
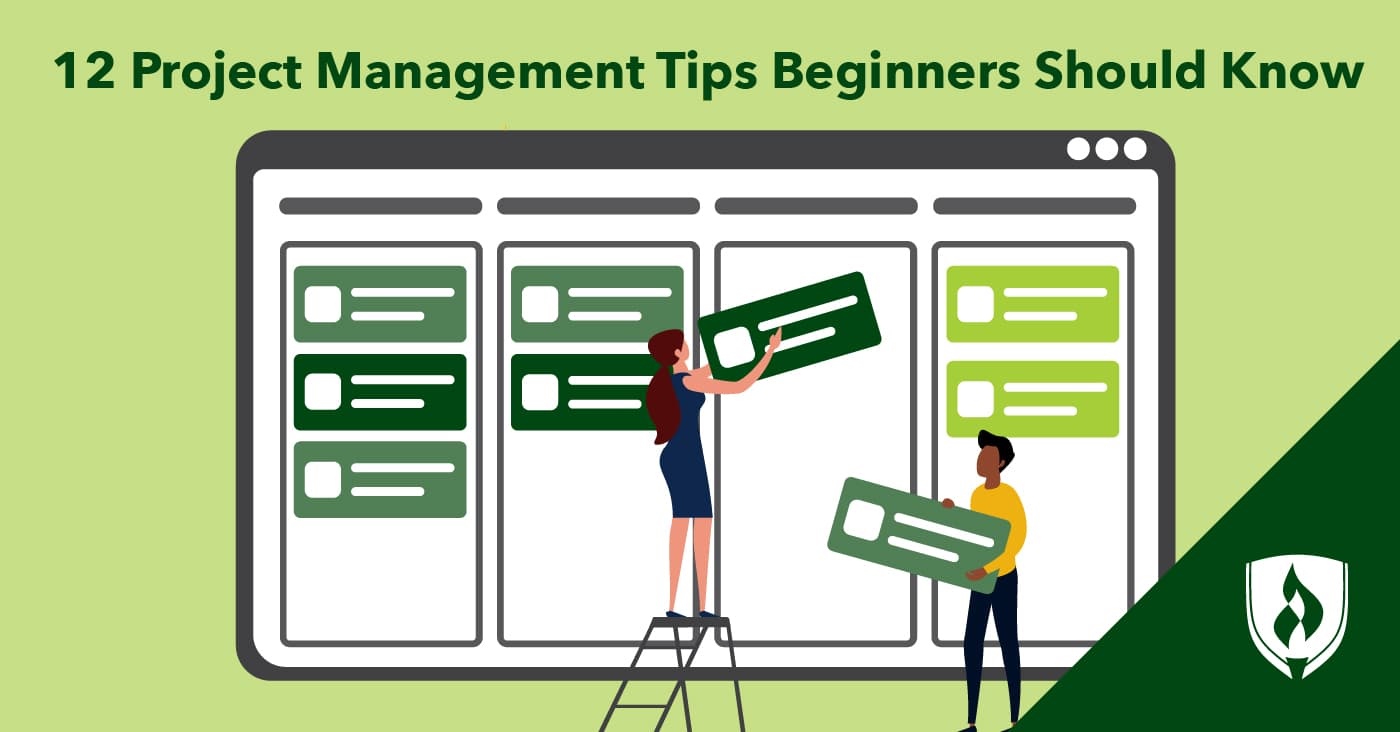
Middle managers should ensure that they have a good understanding of all involved parties and that they develop respect among them. It can be difficult as they may have to manage multiple stakeholders and their time. Therefore, they will need to prioritize their tasks and ensure that all of their needs are met.
Tools for middle managers to collaborate
In organizations, middle managers play an important role. Their primary job is to keep track project progress, transfer information among teams, as well as act as a liaison between junior staff and senior leaders. But communication is more difficult when working remotely. There are many tools that help middle managers to collaborate more effectively.
Many middle managers are required to attend a lot of meetings. This can consume up to 35%. This means that they are often limited in their time for other work. A high cognitive load also results from video communication. This can cause burnout.
Communication skills
Effective communication skills are vital to the success of middle managers. They have to work closely with senior managers and frontline employees. This can be a difficult role. It is possible to build trust between colleagues and improve their influence, engagement and performance.
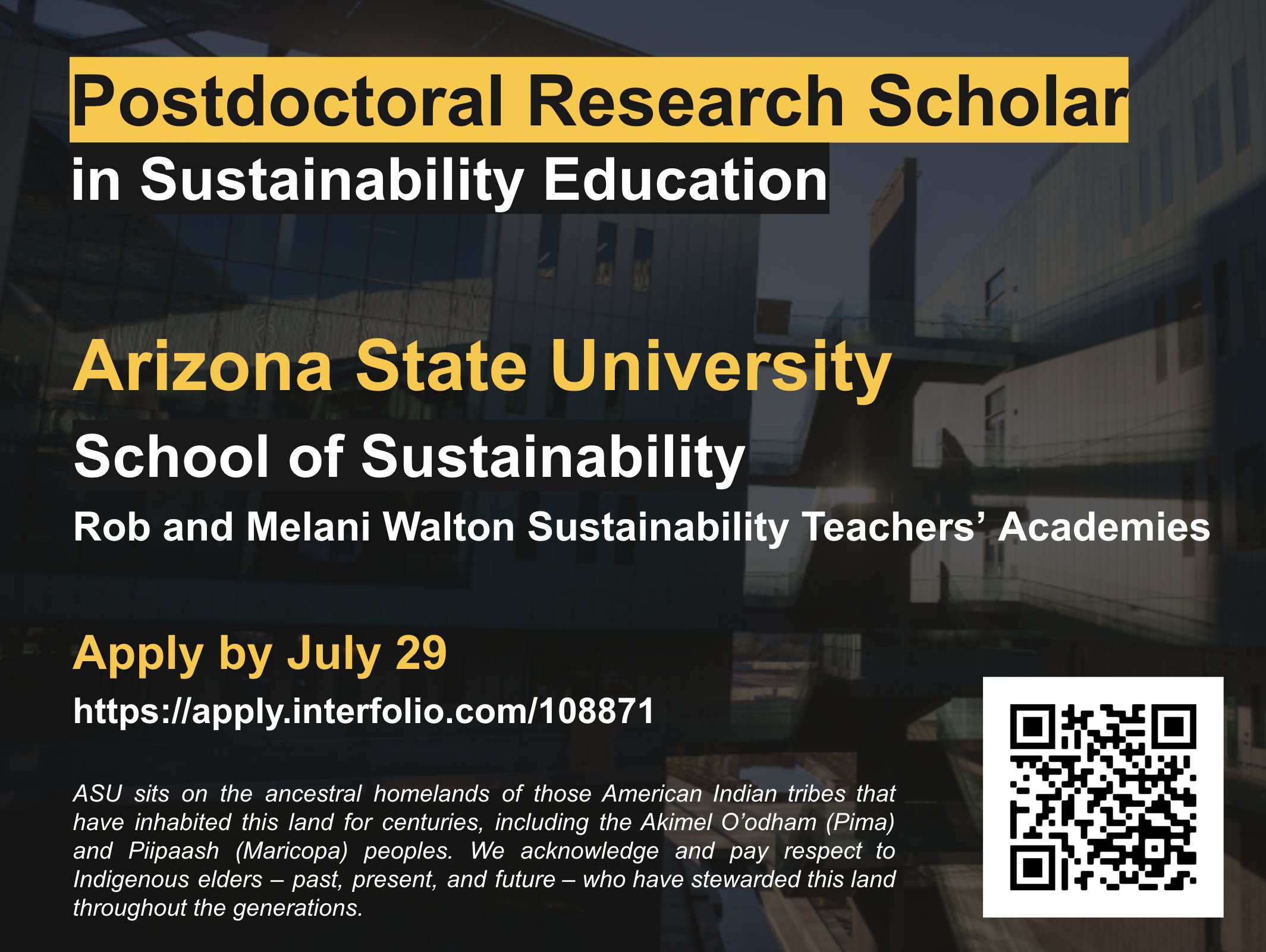
Communication skills in middle management can be crucial in any industry. Middle managers are able to interact with employees directly, unlike senior administrators. It is important for them to be able communicate both verbally and in writing. To avoid miscommunications and errors, middle managers need to be able communicate clearly and effectively.
FAQ
What are the three main management styles you can use?
There are three main management styles: participative, laissez-faire and authoritarian. Each style has its own strengths and weaknesses. Which style do YOU prefer? Why?
Autoritarian - The leader sets direction and expects everyone else to follow it. This style works well if an organization is large and stable.
Laissez-faire - The leader allows each individual to decide for him/herself. This style is best when the organization has a small but dynamic group.
Participative – Leaders are open to suggestions and ideas from everyone. This style is best for small organizations where everyone feels valued.
What is the meaning of "project management?"
We mean managing the activities involved in carrying out a project.
This includes defining the scope, identifying the requirements and preparing the budget. We also organize the project team, schedule the work, monitor progress, evaluate results, and close the project.
How do you effectively manage employees?
Effectively managing employees means making sure they are productive and happy.
This also involves setting clear expectations and monitoring their performance.
Managers need to establish clear goals for their team and for themselves.
They should communicate clearly with employees. They should also ensure that they both reward high performers and discipline those who are not performing to their standards.
They should also keep records of all activities within their team. These include:
-
What was the result?
-
What was the work involved?
-
Who did it all?
-
It was done!
-
Why it was done?
This information can be used to monitor performance and evaluate results.
What is Six Sigma?
It is a way to improve quality that places emphasis on customer service and continuous learning. The goal is to eliminate defects by using statistical techniques.
Motorola's 1986 efforts to improve manufacturing process efficiency led to the creation of Six Sigma.
The idea quickly spread in the industry. Many organizations today use six-sigma methods to improve product design and production, delivery and customer service.
Why is Six Sigma so popular?
Six Sigma is easy and can deliver significant results. It also provides a framework for measuring improvements and helps companies focus on what matters most.
Statistics
- Hire the top business lawyers and save up to 60% on legal fees (upcounsel.com)
- UpCounsel accepts only the top 5 percent of lawyers on its site. (upcounsel.com)
- As of 2020, personal bankers or tellers make an average of $32,620 per year, according to the BLS. (wgu.edu)
- The average salary for financial advisors in 2021 is around $60,000 per year, with the top 10% of the profession making more than $111,000 per year. (wgu.edu)
- Your choice in Step 5 may very likely be the same or similar to the alternative you placed at the top of your list at the end of Step 4. (umassd.edu)
External Links
How To
How do I do the Kaizen Method?
Kaizen means continuous improvement. Kaizen is a Japanese concept that encourages constant improvement by small incremental changes. It's a team effort to continuously improve processes.
Kaizen is one of Lean Manufacturing's most efficient methods. This concept requires employees to identify and solve problems during manufacturing before they become major issues. This improves the quality of products, while reducing the cost.
Kaizen is an approach to making every worker aware and alert to what is happening around them. To prevent problems from happening, any problem should be addressed immediately. If someone is aware of a problem at work, he/she should inform his/her manager immediately.
Kaizen follows a set of principles. Always start with the end product in mind and work our way back to the beginning. To improve our factory, for example, we need to fix the machines that produce the final product. Then, we fix the machines that produce components and then the ones that produce raw materials. Then we fix the workers, who directly work with these machines.
This method is known as kaizen because it focuses upon improving every aspect of the process step by step. Once the factory is fixed, we return to the original site and work our way back until we get there.
How to measure kaizen's effectiveness in your business is essential to implement it. There are many methods to assess if kaizen works well. One of these ways is to check the number of defects found on the finished products. Another way is determining how much productivity increased after implementing kaizen.
A good way to determine whether kaizen has been implemented is to ask why. You were trying to save money or obey the law? You really believed it would make you successful?
Suppose you answered yes to any of these questions, congratulations! You're now ready to get started with kaizen.