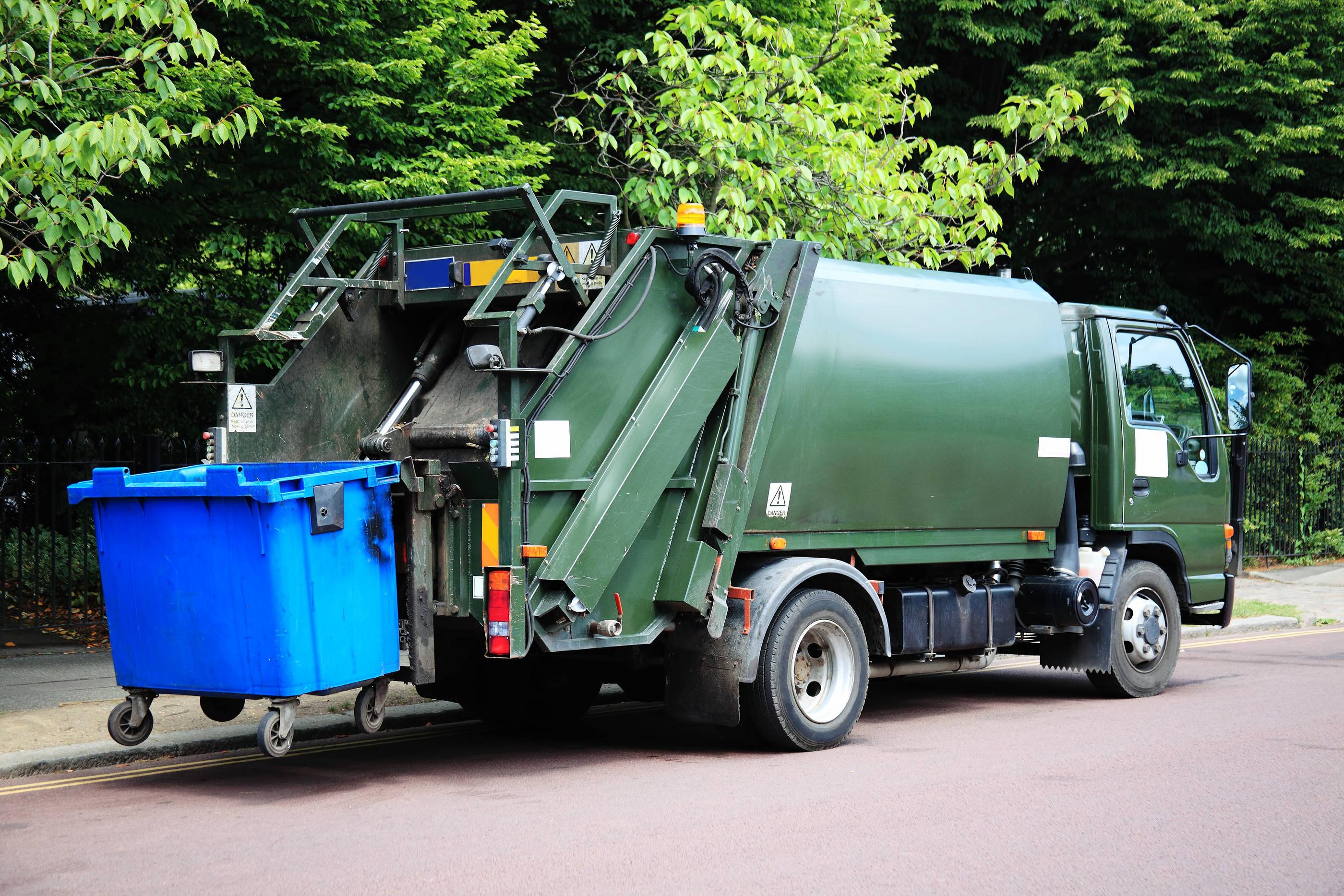
Price risk refers to the possibility that an asset's value will decrease over time. This can happen in any financial instrument. Hedge funds often use a wider definition for price risk due the many market influences that can cause an asset's price decrease. Hedging can be crucial in order to make a profitable investment or one that goes sour.
Investments
When investing, price risk should be considered. In the case of financial instruments, such as stocks, equities, or commodities, a share's price may rise or fall over time. Investors may lose some or all of their investment due to this fluctuation. Market trends and changes can also cause share prices fluctuations. This risk is often overlooked but is incredibly important to investing.
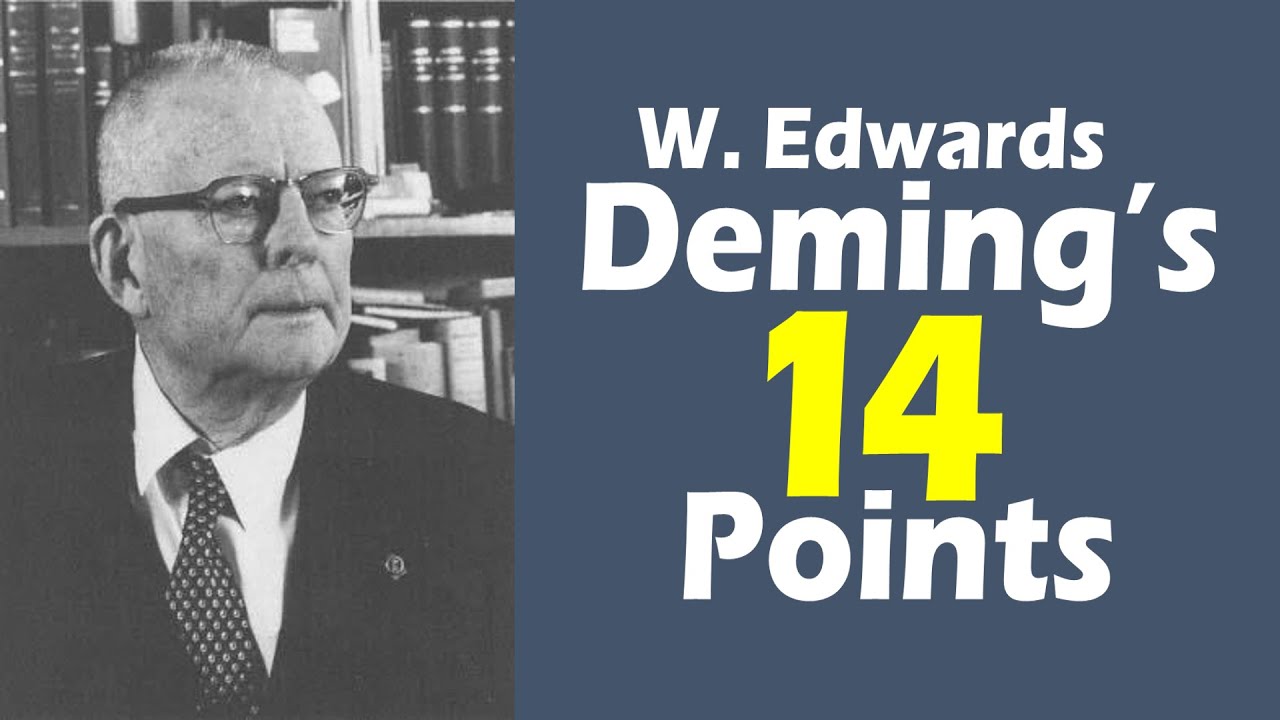
Commodities
As with any investment, there are certain risks associated with the price of a commodity. One risk is volatility in price movements. This could be more than for other assets. Metal prices, for instance, can move by as much as 30 percent. The price risk associated commodities is more complex than that of other financial assets.
Foreign exchange
The currency market is exceptionally volatile right now, largely due to a wide range of factors. These include Brexit and the COVID-19 flu pandemic. This volatility represents a significant shift in developed markets which were previously relatively stable during periods that were calm and peaceful.
Financial instruments
This book provides students with a basic understanding of price risk associated with financial instruments. This includes options as well as futures contracts. These contracts require parties to fulfill a specific action. A futures contract would require the buyer to purchase the underlying asset. A buyer can also purchase or sell securities by way of an option.
Leverage
Both individuals and businesses use leverage to make investments. It can be used for many purposes, including to start a new company or to increase shareholder wealth. You can even use it as a way to purchase a home or attend college. But, it is crucial to understand how it should be used.
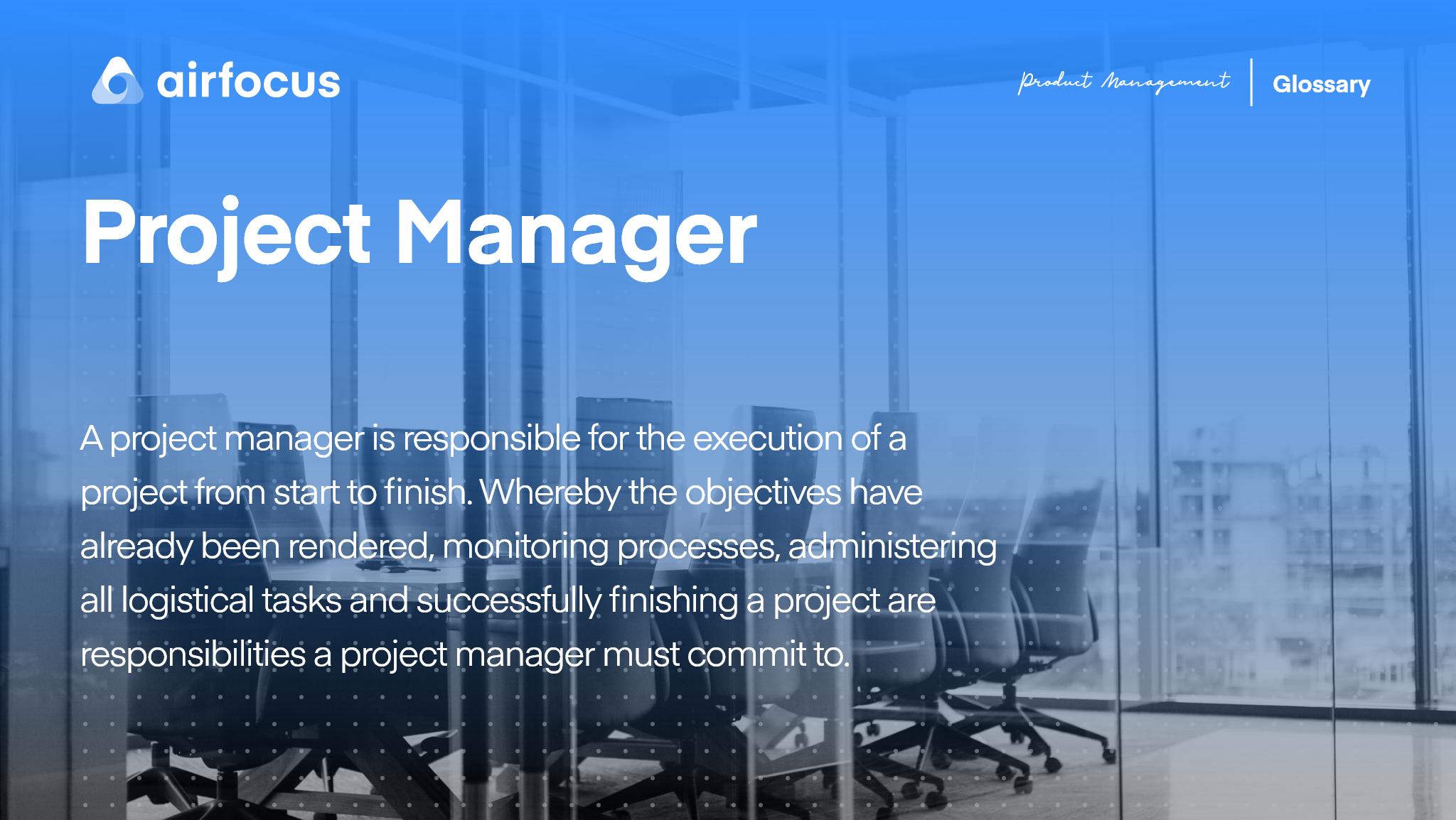
Hedging
The financial strategy of hedge price risk can be used to protect businesses from price changes. This is often done using various financial instruments. This can be used in all areas of business. For example, a manufacturing company that sells its products internationally would hedge against the risk of foreign currency fluctuations. Hedging has its costs.
FAQ
Why is it important that companies use project management methods?
Project management techniques are used in order to ensure projects run smoothly, and that deadlines are met.
This is due to the fact that most businesses rely heavily upon project work in order to produce goods, and services.
These projects require companies to be efficient and effective managers.
Without effective project management, companies may lose money, time, and reputation.
What kind people use Six Sigma?
Six sigma is a common concept for people who have worked in statistics or operations research. It can be used by anyone in any business aspect.
This requires a lot of dedication, so only people with great leadership skills can make the effort to implement it.
What is a basic management tool that can be used for decision-making?
A decision matrix can be a simple, but effective tool to assist managers in making decisions. It allows them to think through all possible options.
A decision matrix is a way of representing alternatives as rows and columns. It is easy to see how each option affects the other options.
The boxes on the left hand side of this matrix represent four possible choices. Each box represents one option. The top row displays the current situation, and the bottom row shows what might happen if nothing is done.
The effect of choosing Option 1 can be seen in column middle. In this example, it would lead to an increase in sales of between $2 million and $3 million.
These are the results of selecting Options 2 or 3. These positive changes result in increased sales of $1 million and $500,000. These changes can also have negative effects. Option 2 can increase costs by $100 million, while Option 3 can reduce profits by $200,000.
Finally, the last column shows the results of choosing Option 4. This results in a decrease of sales by $1,000,000
A decision matrix has the advantage that you don’t have to remember where numbers belong. You just look at the cells and know immediately whether any given a choice is better than another.
This is because the matrix has already taken care of the hard work for you. It's simply a matter of comparing the numbers in the relevant cells.
Here's a sample of how you might use decision matrixes in your business.
It is up to you to decide whether to spend more money on advertising. This will allow you to increase your revenue by $5000 per month. However, additional expenses of $10 000 per month will be incurred.
Look at the cell immediately below the one that states "Advertising" to calculate the net investment in advertising. It's $15,000. Advertising is more valuable than its costs.
What is the difference between TQM and Six Sigma?
The main difference in these two quality management tools lies in the fact that six sigma is focused on eliminating defects and total quality management (TQM), emphasizes improving processes and reducing costs.
Six Sigma stands for continuous improvement. It emphasizes the elimination of defects by using statistical methods such as control charts, p-charts, and Pareto analysis.
This method has the goal to reduce variation of product output. This is accomplished by identifying the root cause of problems and fixing them.
Total quality management includes monitoring and measuring all aspects of an organization's performance. It also includes training employees to improve performance.
It is often used as a strategy to increase productivity.
Statistics
- Your choice in Step 5 may very likely be the same or similar to the alternative you placed at the top of your list at the end of Step 4. (umassd.edu)
- Our program is 100% engineered for your success. (online.uc.edu)
- As of 2020, personal bankers or tellers make an average of $32,620 per year, according to the BLS. (wgu.edu)
- The average salary for financial advisors in 2021 is around $60,000 per year, with the top 10% of the profession making more than $111,000 per year. (wgu.edu)
- UpCounsel accepts only the top 5 percent of lawyers on its site. (upcounsel.com)
External Links
How To
What is Lean Manufacturing?
Lean Manufacturing processes are used to reduce waste and improve efficiency through structured methods. They were developed by Toyota Motor Corporation in Japan during the 1980s. The main goal was to produce products at lower costs while maintaining quality. Lean manufacturing is about eliminating redundant steps and activities from the manufacturing process. It is made up of five elements: continuous improvement, continuous improvement, just in-time, continuous change, and 5S. Pull systems are able to produce exactly what the customer requires without extra work. Continuous improvement is the continuous improvement of existing processes. Just-in–time refers when components or materials are delivered immediately to their intended destination. Kaizen stands for continuous improvement. Kaizen can be described as a process of making small improvements continuously. The 5S acronym stands for sort in order, shine standardize and maintain. These five elements can be combined to achieve the best possible results.
Lean Production System
Six key concepts are the basis of lean production:
-
Flow: The goal is to move material and information as close as possible from customers.
-
Value stream mapping - break down each stage of a process into discrete tasks and create a flowchart of the entire process;
-
Five S's – Sort, Put In Order Shine, Standardize and Sustain
-
Kanban – visual signals like colored tape, stickers or other visual cues are used to keep track inventory.
-
Theory of constraints: identify bottlenecks in your process and eliminate them using lean tools, such as kanban board.
-
Just-intime - Order components and materials at your location right on the spot.
-
Continuous improvement is making incremental improvements to your process, rather than trying to overhaul it all at once.