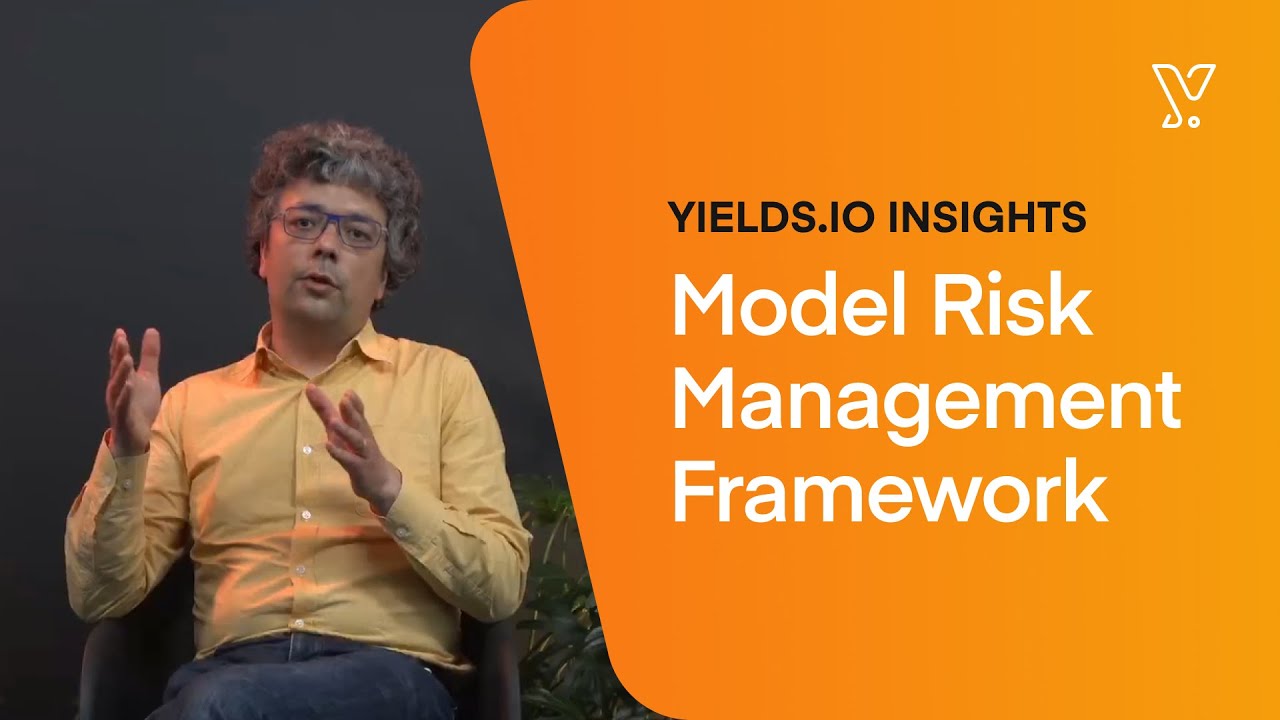
There are four fundamental management perspectives. These perspectives are Theory and Function, Historical Development, Future Trends, and Function. This article will cover each of these perspectives. Each perspective has both its benefits and drawbacks. It is important to understand the difference between each perspective. This will allow you to pick the one that best suits you and your preferences. Here are some examples.
Theories of management
Theories of management are important in determining the appropriate management strategy for an organization. Although each theory is different, they all address the same management issue: organizational behavior. While no single theory is best suited for every organization, a combination of theories can produce more effective results. Modern organizations are more flexible because they use a variety of theories.
The theories of management can be applied in many settings, such as project management or general management. They can be seen as concise pieces of knowledge that allow novices to perform the same tasks as an expert in project management. However, they are most effective when applied in a small project setting, where theory-related issues can be solved without wider penalties. However, they can lead to serious performance problems and other issues in large projects that could have avoided with better management.
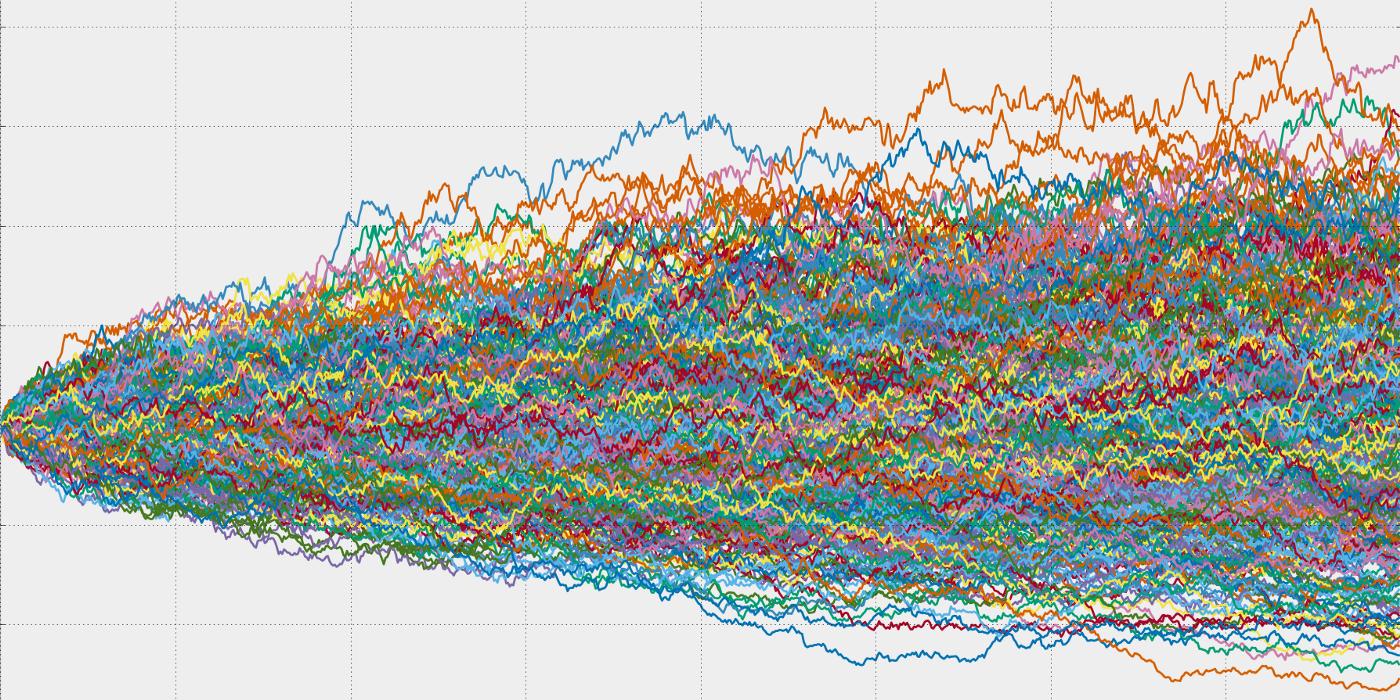
Management functions
To ensure that an organisation succeeds, it is important for them to perform their functions. These include planning, identifying the tasks, monitoring and correcting any problems. Management is a key role in any organization. This includes achieving profit goals and maintaining market share. Managers are responsible for making the decisions, implementing strategies, and monitoring the progress of all parts of the organization.
Planning is the first step in the managerial process. It involves defining and assessing the goals. It requires analytical skills and an understanding of past and current trends, as well as the ability to develop and implement future strategies. An organisation can reach its goals if these functions are performed correctly.
Historical development
Management has evolved over the years with new theories that emphasize the human factor. Douglas McGregor, author of "Theory Y," is a prime example. It also altered the traditional definition of what executives do. They no longer have to be masters of the organisation but can now act more like coaches. The emphasis on the human element and emotional intelligence in management was changed when organizational theorists started to investigate the topic.
The Industrial Revolution was the catalyst for intense debate regarding management theory. This was a crucial moment in management history. The ensuing changes led to the emergence of six main management theories. Each theory focuses on a different aspect of management.
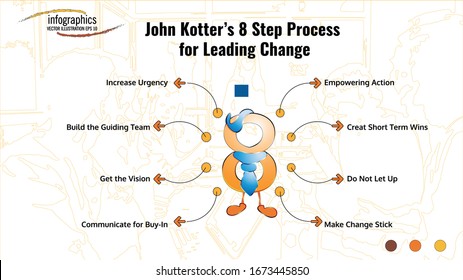
Future trends
The future of management is shaped by a series of trends that are influencing the work environment. One of these trends concerns the changing role that managers play. This change requires managers be more flexible and agile. Flexibility is becoming more mainstream in the UK. More than half of managers expect flexible working to be the norm within five years, while half believe that their direct reports are working more flexible than they were five years ago.
The increasing importance of working relations is one trend that is affecting the sector of management. More than half of managers recognise this as a future trend and believe that they are more important now than five years ago. This trend is being supported by the rise of flexible working environments. Also, the recent economic crisis has forced some people to place more emphasis on personal relationships and trust. These new trends are a great way for companies to retain and develop their employees.
FAQ
What is Six Sigma and how can it help you?
It's a method for quality improvement that focuses on customer service as well as continuous learning. The objective is to eliminate all defects through statistical methods.
Motorola developed Six Sigma in 1986 to help improve its manufacturing processes.
This idea quickly spread throughout the industry. Today, many organizations use six sigma methods for product design, production and delivery.
How can a manager improve his/her managerial skills?
Through demonstrating good management skills at every opportunity
Managers should monitor the performance and progress of their subordinates.
If you notice your subordinate isn't performing up to par, you must take action quickly.
You must be able to spot what is lacking and how you can improve it.
What are some of the common mistakes made by managers?
Managers can make their jobs more difficult than necessary.
They may not assign enough responsibilities to staff members and provide them with inadequate support.
Many managers lack the communication skills to motivate and lead their employees.
Some managers set unrealistic expectations for their staff.
Managers may choose to solve every problem all by themselves, instead of delegating to others.
Statistics
- Our program is 100% engineered for your success. (online.uc.edu)
- 100% of the courses are offered online, and no campus visits are required — a big time-saver for you. (online.uc.edu)
- Your choice in Step 5 may very likely be the same or similar to the alternative you placed at the top of your list at the end of Step 4. (umassd.edu)
- UpCounsel accepts only the top 5 percent of lawyers on its site. (upcounsel.com)
- This field is expected to grow about 7% by 2028, a bit faster than the national average for job growth. (wgu.edu)
External Links
How To
How can Lean Manufacturing be done?
Lean Manufacturing processes are used to reduce waste and improve efficiency through structured methods. They were created in Japan by Toyota Motor Corporation during the 1980s. The goal was to produce quality products at lower cost. Lean manufacturing is about eliminating redundant steps and activities from the manufacturing process. It is composed of five fundamental elements: continuous improvement; pull systems, continuous improvements, just-in–time, kaizen, continuous change, and 5S. Pull systems involve producing only what the customer wants without any extra work. Continuous improvement involves constantly improving upon existing processes. Just-in-time refers to when components and materials are delivered directly to the point where they are needed. Kaizen means continuous improvement. Kaizen involves making small changes and improving continuously. Finally, 5S stands for sort, set in order, shine, standardize, and sustain. These five elements are used together to ensure the best possible results.
Lean Production System
Six key concepts are the basis of lean production:
-
Flow - focus on moving material and information as close to customers as possible;
-
Value stream mapping - Break down each stage in a process into distinct tasks and create an overview of the whole process.
-
Five S’s - Sorted, In Order. Shine. Standardize. And Sustain.
-
Kanban - visual cues such as stickers or colored tape can be used to track inventory.
-
Theory of constraints: Identify bottlenecks and use lean tools such as kanban boards to eliminate them.
-
Just-in-time delivery - Deliver components and materials right to your point of use.
-
Continuous improvement - make incremental improvements to the process rather than overhauling it all at once.