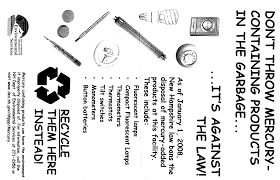
CSCMP is for Certified Systems and Communications Manager. It's a valuable certification for professionals in systems and communications. CSCMP consists 160 questions and takes 4 hours to complete. It is given by an independent 3rd-party company called Pearson VUE, and there are testing centers worldwide. The exam is proctored onsite and provides pass/fail status to the taker.
Academic membership
Academic membership in CSCM is open to academics who hold full-time positions at accredited colleges or universities. Membership requires $175 annually and offers opportunities to develop course content and participate in collaborative forums. It also allows members to network with other colleagues in the field. For more information on how to become a member, contact us.
Cost of membership
The Council of Supply Chain Management Professionals was established to connect, educate, and develop supply chain professionals all over the world. For $149, you can join the group for six months and gain access to many of the organization's member events and benefits. Young professionals can also sign up for a six-month membership for only $88. Both membership options will expire on August 31, 2021.
A CSCMP membership includes access to the organization's resources, which include leading research and surveys. Members get first access to these research and actionable insights. The organization hosts webinars which are available to all members at no cost. CSCMP Membership allows you to find out more about supply chain management, and how to improve the business operations.
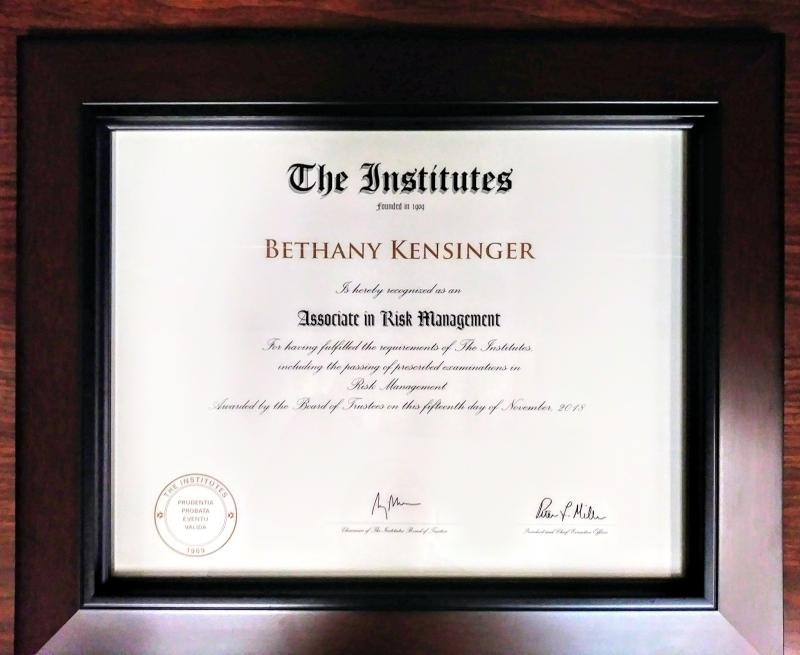
CSCMP members are made by passing the SCMP 2 exam. Within one year of paying your membership fees, you can take this exam. A confirmation email will be sent to you approximately one week before your scheduled test date.
FAQ
What are the steps involved in making a decision in management?
Managers face complex and multifaceted decision-making challenges. It includes many factors such as analysis, strategy planning, implementation and measurement. Evaluation, feedback and feedback are just some of the other factors.
The key thing to remember when managing people is that they are human beings just as you are and therefore make mistakes. As such, there are always opportunities for improvement, especially when you put in the effort to improve yourself.
In this video, we explain what the decision-making process looks like in Management. We will explain the importance of different types decisions and how every manager can make them. The following topics will be covered.
What are the most important management skills?
Management skills are essential for any business owner, whether they're running a small local store or an international corporation. These skills include the ability of managing people, finances, time, space, and other factors.
When you need to manage people, set goals, lead teams, motivate them, solve problems, develop policies and procedures and manage change, management skills are essential.
There are so many managerial tasks!
How do you manage employees effectively?
The key to effective management of employees is ensuring their happiness and productivity.
It also means having clear expectations of their behavior and keeping track of their performance.
To do this successfully, managers need to set clear goals for themselves and for their teams.
They need to communicate clearly and openly with staff members. They need to communicate clearly with their staff.
They must also keep track of the activities of their team. These include:
-
What was the result?
-
What was the work involved?
-
Who did it, anyway?
-
What was the moment it was completed?
-
Why it was done?
This information can be used for monitoring performance and evaluating results.
What is the difference between TQM and Six Sigma?
The main difference in these two quality management tools lies in the fact that six sigma is focused on eliminating defects and total quality management (TQM), emphasizes improving processes and reducing costs.
Six Sigma is an approach for continuous improvement. This approach emphasizes eliminating defects through statistical methods like control charts, Pareto analysis, and p-charts.
This method attempts to reduce variations in product output. This is done by identifying and correcting the root causes of problems.
Total quality management involves measuring and monitoring all aspects of the organization. Training employees is also part of total quality management.
It is commonly used as a strategy for increasing productivity.
It seems so difficult sometimes to make sound business decisions.
Complex systems with many moving parts are the hallmark of businesses. Their leaders must manage multiple priorities, as well as dealing with uncertainty.
To make good decisions, you must understand how these factors affect the entire system.
It is important to consider the functions and reasons for each part of the system. It is important to then consider how the individual pieces relate to each other.
It is also worth asking yourself if you have any unspoken assumptions about how you have been doing things. If not, you might want to revisit them.
Try asking for help from another person if you're still stuck. You might find their perspective is different from yours and they may have insight that can help you find the solution.
How does Six Sigma work?
Six Sigma uses statistical analysis for problems to be found, measured, analyzed root causes, corrected, and learned from.
The first step to solving the problem is to identify it.
The next step is to collect data and analyze it in order to identify trends or patterns.
Then corrective actions are taken to solve the problem.
Finally, data is reanalyzed to determine whether the problem has been eliminated.
This cycle continues until there is a solution.
Statistics
- The average salary for financial advisors in 2021 is around $60,000 per year, with the top 10% of the profession making more than $111,000 per year. (wgu.edu)
- Hire the top business lawyers and save up to 60% on legal fees (upcounsel.com)
- Your choice in Step 5 may very likely be the same or similar to the alternative you placed at the top of your list at the end of Step 4. (umassd.edu)
- Our program is 100% engineered for your success. (online.uc.edu)
- This field is expected to grow about 7% by 2028, a bit faster than the national average for job growth. (wgu.edu)
External Links
How To
What is Lean Manufacturing?
Lean Manufacturing methods are used to reduce waste through structured processes. They were developed by Toyota Motor Corporation in Japan during the 1980s. It was designed to produce high-quality products at lower prices while maintaining their quality. Lean manufacturing seeks to eliminate unnecessary steps and activities in the production process. It is made up of five elements: continuous improvement, continuous improvement, just in-time, continuous change, and 5S. It is a system that produces only the product the customer requests without additional work. Continuous improvement refers to continuously improving existing processes. Just-in time refers to components and materials being delivered right at the place they are needed. Kaizen is continuous improvement. This can be achieved by making small, incremental changes every day. The 5S acronym stands for sort in order, shine standardize and maintain. To achieve the best results, these five elements must be used together.
Lean Production System
The lean production system is based on six key concepts:
-
Flow - focuses on moving information and materials as close to customers as possible.
-
Value stream mapping- This allows you to break down each step of a process and create a flowchart detailing the entire process.
-
Five S's - Sort, Set In Order, Shine, Standardize, and Sustain;
-
Kanban - visual cues such as stickers or colored tape can be used to track inventory.
-
Theory of constraints - identify bottlenecks in the process and eliminate them using lean tools like kanban boards;
-
Just-in-time - deliver components and materials directly to the point of use;
-
Continuous improvement - make incremental improvements to the process rather than overhauling it all at once.