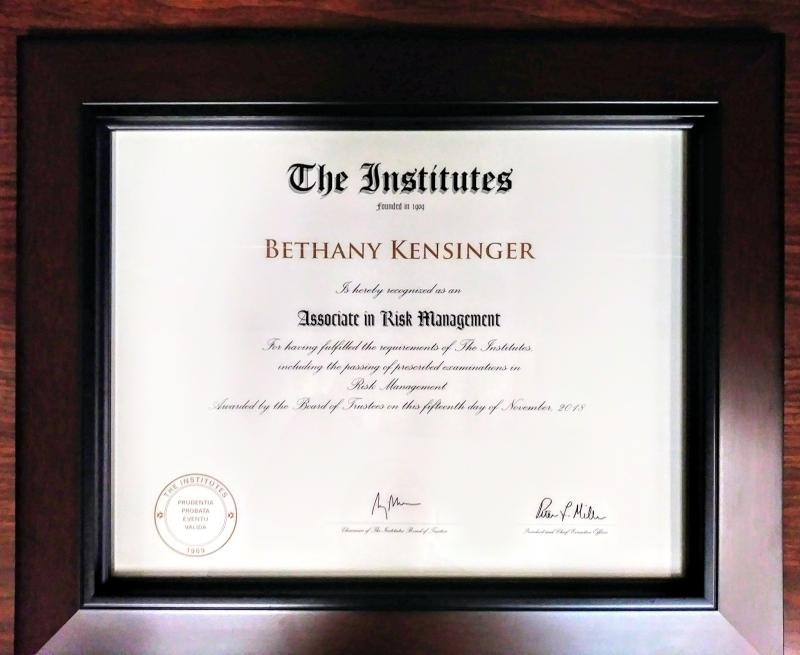
Model risk is a risk that arises from the use of insufficiently accurate models. This risk is often associated to the valuation of financial security. It is not an easy risk to manage. As its name suggests, model risk arises from inaccurate and unrealistic assumptions. It is an operational risk. Financial institutions should be aware that model risk can still be a concern.
Model risk is a subset of operational risk
Model risk is a risk related to the use of predictive modeling in the business process. While these models can be of great value, they also carry a higher level of risk, especially if they are not built properly or if they fail to make accurate predictions. Bad models can have severe consequences, so it is important to properly manage this risk. Fortunately, automated machine learning can help to reduce this risk.
Model risk mainly affects the firm that creates and uses the model, rather than the model itself. If the model is incomplete or faulty, it could lead to incorrect or erroneous results that can impact the business's financial performance.
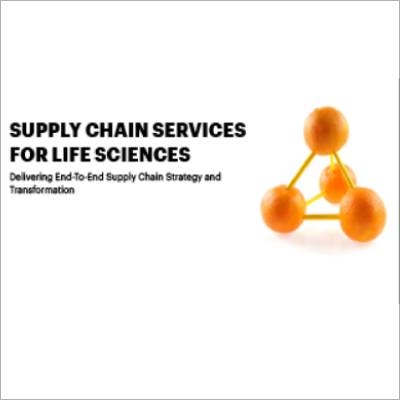
It is caused because of incorrect and unrealistic assumptions
Improper assumptions and data can result in inaccurate model results and incorrect decisions. These errors can lead to significant financial loss and poor decision-making by an organization. They also damage a company’s reputation. Incorrect models affect various industries. Incorrect models can lead to inaccurate predictions about the possibility of terrorist attacks on planes or fraudulent credit card transactions. Bad data and programming errors can lead to model errors.
Failure of a model could result in financial loss, regulatory sanctions, and reputational damage. The risk associated with model failure can be managed by enforcing governance policies and monitoring models. However, model developers bear the responsibility for identifying model failures and assessing them.
It's difficult to manage.
There is a rising risk that predictive models will be integrated into business processes. The potential risks of a poor model can be devastating. As such, Model Risk Management is essential to managing such risk. Organizations can reduce the risk associated to these models through proper governance and process, which will allow them to achieve sustainable growth in all verticals.
Model risk management is only possible when there is a systematic model development and implementation process. Model governance policies should also be used for model risk management. Every employee of the organization is responsible for understanding the risks associated model failure. Enterprise MLOps includes model risk management.
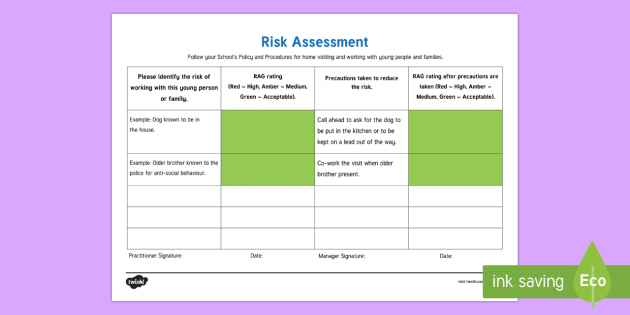
While there are a variety of ways to minimize model risk, it is difficult to completely eliminate it. You can manage it with other tools like monitoring model performance and analyzing model results in other ways. A solid governance framework is essential for model risk management. It must identify relevant risks and allocate resources accordingly. It should also include a team of internal audit professionals who can review model risk management practices to ensure they adhere to acceptable policies.
FAQ
What are the main management skills?
Management skills are essential for any business owner, whether they're running a small local store or an international corporation. They are the ability to manage people and finances, space, money, and other factors.
You will need management skills to set goals and objectives, plan strategies, motivate employees, resolve problems, create policies and procedures, and manage change.
As you can see there is no end to the number of managerial tasks.
What is the difference between Six Sigma Six Sigma and TQM?
The major difference between the two tools for quality management is that six Sigma focuses on eliminating defect while total quality control (TQM), on improving processes and decreasing costs.
Six Sigma is an approach for continuous improvement. It emphasizes the elimination or minimization of defects through statistical methods such control charts and p charts.
This method aims to reduce variation in product production. This is done by identifying root causes and rectifying them.
Total quality management refers to the monitoring and measurement of all aspects in an organization. It also includes training employees to improve performance.
It is frequently used as an approach to increasing productivity.
What are the 4 major functions of management
Management is responsible for planning, organizing, directing, and controlling people and resources. Management also involves setting goals and developing policies.
Management helps an organization achieve its objectives by providing direction, coordination, control, leadership, motivation, supervision, training, and evaluation.
The following are the four core functions of management
Planning – Planning involves deciding what needs to happen.
Organizing: Organizing refers to deciding how things should work.
Directing - This refers to getting people follow instructions.
Controlling: Controlling refers to making sure that people do what they are supposed to.
Statistics
- Hire the top business lawyers and save up to 60% on legal fees (upcounsel.com)
- The BLS says that financial services jobs like banking are expected to grow 4% by 2030, about as fast as the national average. (wgu.edu)
- Your choice in Step 5 may very likely be the same or similar to the alternative you placed at the top of your list at the end of Step 4. (umassd.edu)
- Our program is 100% engineered for your success. (online.uc.edu)
- 100% of the courses are offered online, and no campus visits are required — a big time-saver for you. (online.uc.edu)
External Links
How To
What is Lean Manufacturing?
Lean Manufacturing processes are used to reduce waste and improve efficiency through structured methods. These processes were created by Toyota Motor Corporation, Japan in the 1980s. The primary goal was to make products with lower costs and maintain high quality. Lean manufacturing focuses on eliminating unnecessary steps and activities from the production process. It has five components: continuous improvement and pull systems; just-in time; continuous change; and kaizen (continuous innovation). The production of only what the customer needs without extra work is called pull systems. Continuous improvement is constantly improving upon existing processes. Just-intime refers the time components and materials arrive at the exact place where they are needed. Kaizen is continuous improvement. This can be achieved by making small, incremental changes every day. Fifth, the 5S stand for sort, set up in order to shine, standardize, maintain, and standardize. These five elements can be combined to achieve the best possible results.
Lean Production System
The lean production system is based on six key concepts:
-
Flow - The focus is on moving information and material as close as possible to customers.
-
Value stream mapping - break down each stage of a process into discrete tasks and create a flowchart of the entire process;
-
Five S's: Sort, Shine Standardize, Sustain, Set In Order, Shine and Shine
-
Kanban - visual cues such as stickers or colored tape can be used to track inventory.
-
Theory of Constraints - Identify bottlenecks in the process, and eliminate them using lean tools such kanban boards.
-
Just-in-time delivery - Deliver components and materials right to your point of use.
-
Continuous improvement: Make incremental improvements to the process instead of overhauling it completely.