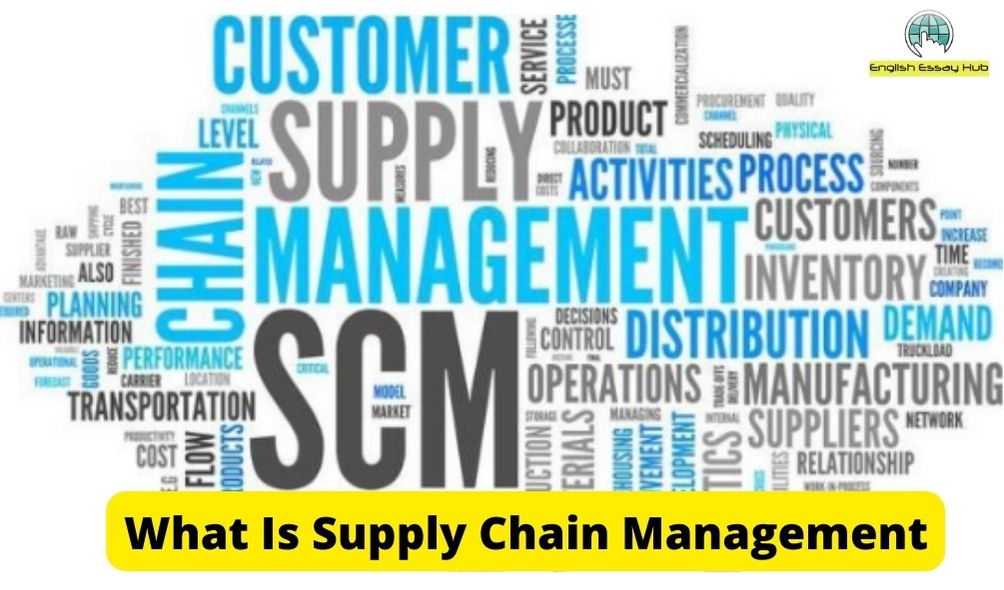
It is a complex process to engineer a building. There are many types of engineers in the construction industry. There are several types of engineers in the construction industry, including Civil engineers. These engineers create construction plans and supervise their execution. They may also work with manual labor and other engineers. As energy-efficient buildings become increasingly important to clients, engineers are often asked to propose alternative methods of generating power. One common method is to use solar energy.
Civil engineers
Civil engineers are professionals who work on construction projects. They design, plan, and build projects. Additionally, they test finished products to ensure that everything is working as it should. They spend much of their time on-site, dealing with many challenges and keeping pace with the progress. Their goal is to make a structure that is both safe and sustainable. Civil engineers are in high demand, and many people seek a career in this field.
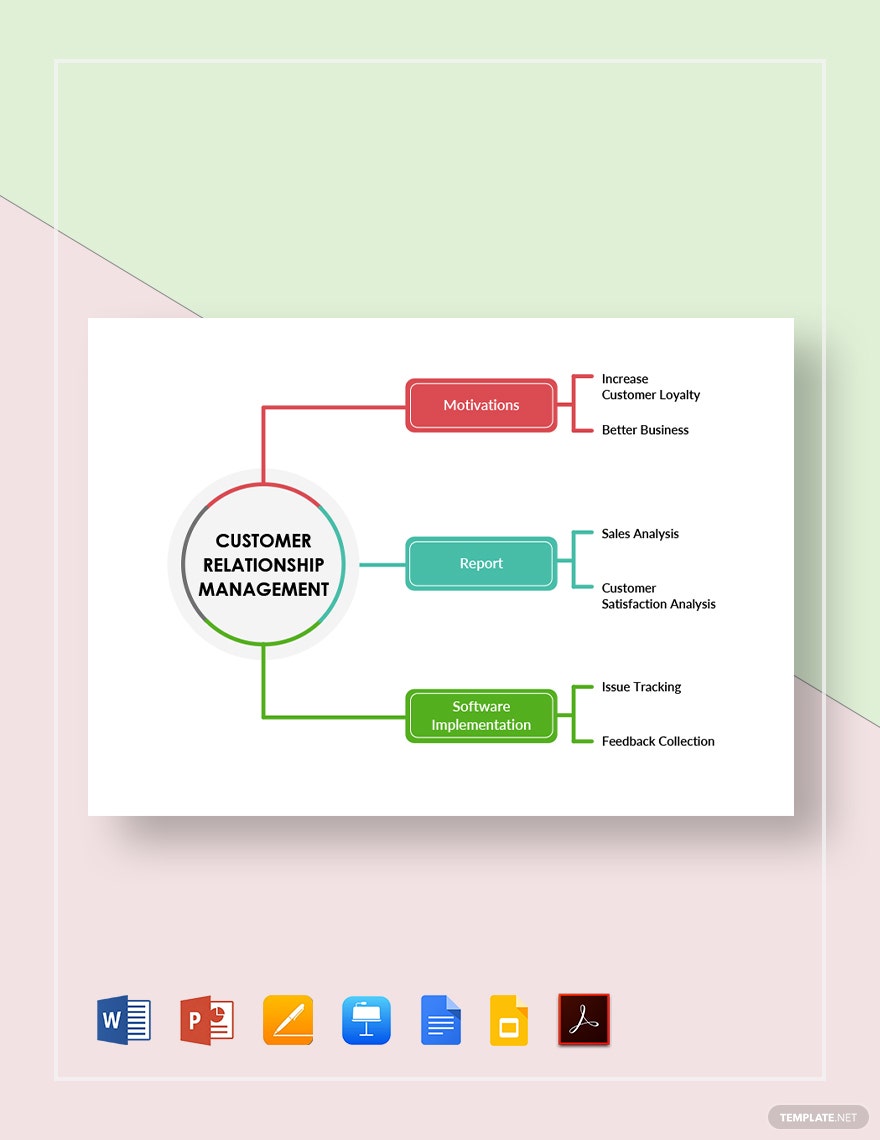
Structural engineers
From one project to the next, structural engineers play a variety of roles in construction. The role includes the analysis of basic building components and liaison with other members of project teams. This role also includes inspecting and monitoring the work of contractors on a project. It may also include evaluating the foundation's properties and conditions. To ensure that a building is constructed properly, structural engineers can also use computer-aided engineering (CAD).
Electrical engineers
The role of an electrician at a construction site is critical in ensuring safety. They ensure electrical appliances are safe for workers and there are no exposed connections. They also make sure high risk areas aren't accessible. The job requires great time management and communication skills. An electrical engineer must have all the technical and soft skills necessary to maintain a safe construction site. They also have to be knowledgeable about electrical safety regulations and codes.
Fire protection engineers
Fire protection engineers should be knowledgeable about the chemistry, materials, and constructions. They must also understand the interactions of fire and suppression chemicals. They should also be in close contact with legal entities and the public. They need to be familiar with court procedures, including how to create documents, present findings, and conduct studies. Although a Master of Science degree may be desirable, it is not necessary. Research in academia requires only a doctorate. There are many accredited programs in fire protection engineering.
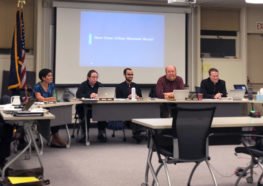
Engineers in environmental engineering
The construction industry is one of the largest end users of natural resources and the largest source of pollutants. The role of environmental engineers in the construction industry is to make it more sustainable and increase its performance. Engineers can optimize construction sites by using life cycle analyses and innovative design to minimize environmental impact. The role of environmental engineers is to transform outdated practices into more sustainable ones. Their expertise will determine the future of construction. Here are the main roles of environmental engineers.
FAQ
What is the difference between leadership and management?
Leadership is about inspiring others. Management is about controlling others.
Leaders inspire followers, while managers direct workers.
A leader inspires others to succeed, while a manager helps workers stay on task.
A leader develops people; a manager manages people.
Six Sigma is so popular.
Six Sigma is simple to implement and can yield significant results. It provides a framework that allows for improvement and helps companies concentrate on what really matters.
What are management concepts?
Management concepts are the fundamental principles and practices that managers use when managing people and their resources. These include topics such as human resource policies and job descriptions, performance assessments, training programs and employee motivation.
What are the steps in the decision-making process in management?
The decision-making process of managers is complicated and multifaceted. It involves many factors, such as analysis and strategy, planning, execution, measurement, evaluation, feedback etc.
The key thing to remember when managing people is that they are human beings just as you are and therefore make mistakes. As such, there is always room for improvement, especially if you're willing to put forth the effort to improve yourself first.
This video shows you how management makes decisions. We will discuss the various types of decisions, and why they are so important. Every manager should be able to make them. These topics are covered in this course:
What are the 3 main management styles?
There are three types of management: participative, laissez faire, and authoritarian. Each style has its advantages and disadvantages. Which style do you prefer? Why?
Authority - The leader is the one who sets the direction and expects everyone in the organization to follow it. This style works well if an organization is large and stable.
Laissez-faire: The leader lets each person decide for themselves. This style is most effective when the organization's size and dynamics are small.
Participative – The leader listens and takes in ideas from all. This approach works best in small organizations where everyone feels valued.
What's the difference between Six Sigma and TQM?
The main difference between these two quality management tools is that six sigma focuses on eliminating defects while total quality management (TQM) focuses on improving processes and reducing costs.
Six Sigma is a methodology for continuous improvement. This method emphasizes eliminating defects using statistical methods such p-charts, control charts, and Pareto analysis.
The goal of this method is to reduce variation in product output. This is done by identifying root causes and rectifying them.
Total quality management refers to the monitoring and measurement of all aspects in an organization. This includes training employees to improve their performance.
It is often used as a strategy to increase productivity.
What is Six Sigma?
Six Sigma uses statistical analyses to locate problems, measure them, analyze root cause, fix problems and learn from the experience.
The first step is to identify the problem.
The next step is to collect data and analyze it in order to identify trends or patterns.
Next, corrective steps are taken to fix the problem.
Finally, data will be reanalyzed to determine if there is an issue.
This cycle continues until the problem is solved.
Statistics
- This field is expected to grow about 7% by 2028, a bit faster than the national average for job growth. (wgu.edu)
- The profession is expected to grow 7% by 2028, a bit faster than the national average. (wgu.edu)
- The BLS says that financial services jobs like banking are expected to grow 4% by 2030, about as fast as the national average. (wgu.edu)
- Your choice in Step 5 may very likely be the same or similar to the alternative you placed at the top of your list at the end of Step 4. (umassd.edu)
- The average salary for financial advisors in 2021 is around $60,000 per year, with the top 10% of the profession making more than $111,000 per year. (wgu.edu)
External Links
How To
How does Lean Manufacturing work?
Lean Manufacturing methods are used to reduce waste through structured processes. They were developed in Japan by Toyota Motor Corporation (in the 1980s). The goal was to produce quality products at lower cost. Lean manufacturing seeks to eliminate unnecessary steps and activities in the production process. It includes five main elements: pull systems (continuous improvement), continuous improvement (just-in-time), kaizen (5S), and continuous change (continuous changes). It is a system that produces only the product the customer requests without additional work. Continuous improvement is the continuous improvement of existing processes. Just-in time refers to components and materials being delivered right at the place they are needed. Kaizen means continuous improvement. Kaizen involves making small changes and improving continuously. The 5S acronym stands for sort in order, shine standardize and maintain. These five elements are used together to ensure the best possible results.
Lean Production System
Six key concepts are the basis of lean production:
-
Flow - focuses on moving information and materials as close to customers as possible.
-
Value stream mapping - Break down each stage in a process into distinct tasks and create an overview of the whole process.
-
Five S's - Sort, Set In Order, Shine, Standardize, and Sustain;
-
Kanban is a visual system that uses visual cues like stickers, colored tape or stickers to keep track and monitor inventory.
-
Theory of constraints: identify bottlenecks in your process and eliminate them using lean tools, such as kanban board.
-
Just-in Time - Send components and material directly to the point-of-use;
-
Continuous improvement - make incremental improvements to the process rather than overhauling it all at once.