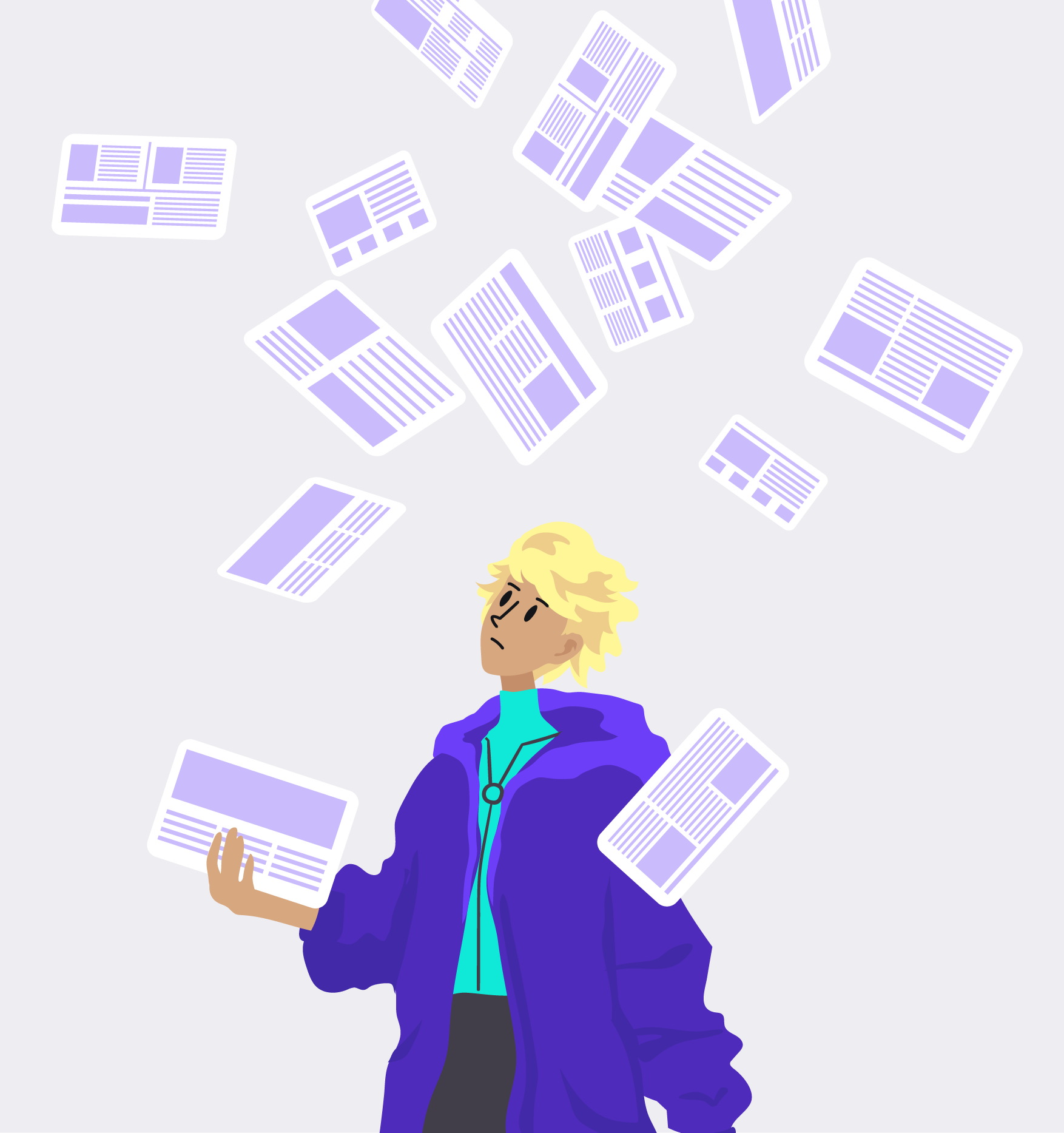
To evaluate the risks an organization faces, risk models can be used. Banks can use many types of models to determine the risks involved in various situations. These models have become more complex with the advent of advanced analytics techniques, like machine learning. These models can now be used for a greater variety of decision-making functions.
Gail model
The Gail risk modeling is an important tool for determining a woman’s risk of breast cancer. It is not designed to diagnose high-risk women, but can be used for estimating breast cancer risk. Although this tool does not replace screening for breast cancer it can help in diagnosing the condition. Gail risk modeling may help more women receive chemoprevention. It can also help to reduce the morbidity and mortality associated with the disease.
Credit risk models
Credit risk models are a way to determine the likelihood of default based on various factors. These include the financial status of the borrower, the consequences of default and macroeconomic factors. The most important part a credit risk model's credit risk is the probability for default. This is calculated by a borrower’s debt-to–income ratio and credit score. These probabilities are calculated by rating agencies and used to determine the interest rate and down payment a borrower must pay.
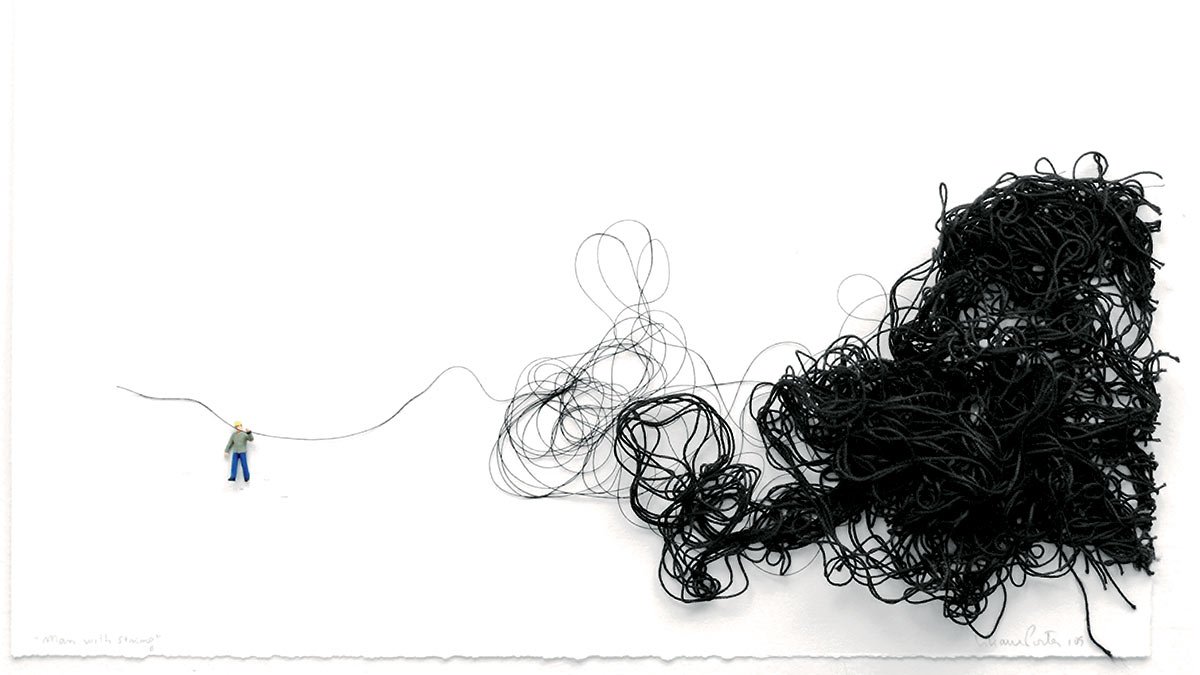
Multistage models
A popular model to understand the origins of cancer is the multistage model. The multistage model suggests that the intrinsic cancer risk is determined by the total number stem cell divisions in at high-risk tissue. This model has been used in cancer research for many years. It is important for the interpretation and prediction of cancer incidence.
Marshall-Olkin coulas
Recent years have seen an increase in the interest in Marshall-Olkin Copulas (MO). These copulas can be described as generalized distributions with an exponential shape. They are often used in extreme value theory and reliability analysis. They are useful when describing a distribution that has a series of independent shocks and are not perfectly distributed.
Errors in dose estimates
Bias in risk models is often caused by errors in dose estimations. These errors can be caused by a variety reasons and will not have the same effect on risk parameter estimates. Some errors can be systematic and affect all dose estimates in the exact same way.
Incorrect assumptions in model outputs
The 2013 risk model overestimated the risk several times when it was applied to modern data and external validation cohorts. In some cases, this overestimation is pronounced for higher-risk patients, while in other cases, it is more pronounced for lower-risk patients, raising the risk of overtreatment. The model outputs also showed discrimination that was suboptimal. C statistics for discrimination cohorts varied from 0.66 to 0.77, while the numbers for derivation cohorts ranged between 71-75.
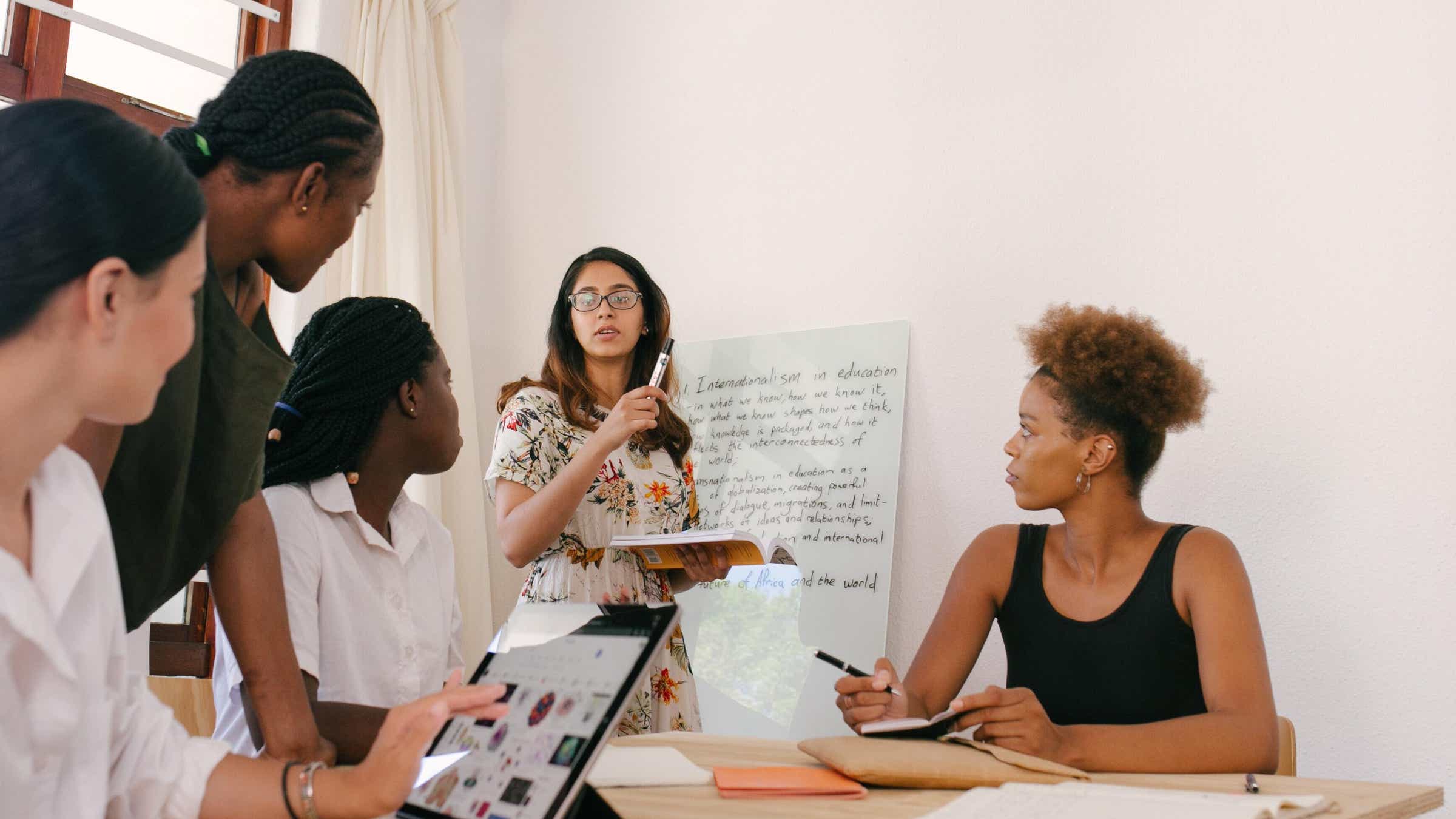
Methods for evaluating model performance
It is important to take into account the precision and accuracy of the model in order to judge its performance. These parameters determine how well a model distinguishes between true or false risks. By adding covariates, a risk modeling model can be made more precise and accurate. The model's application will influence the importance of the scores.
FAQ
What is the difference between leadership and management?
Leadership is about influence. Management is all about controlling others.
Leaders inspire others, managers direct them.
A leader inspires others to succeed, while a manager helps workers stay on task.
A leader develops people; a manager manages people.
What is TQM?
The industrial revolution was when companies realized that they couldn't compete on price alone. This is what sparked the quality movement. They needed to improve quality and efficiency if they were going to remain competitive.
Management developed Total Quality Management to address the need for improvement. It focused on all aspects of an organisation's performance. It included continuous improvement processes, employee involvement, and customer satisfaction.
What are the four main functions of management?
Management is responsible for organizing, managing, directing and controlling people, resources, and other activities. It includes creating policies and procedures, as well setting goals.
Organizations can achieve their goals through management. This includes leadership, coordination, control and motivation.
The following are the four core functions of management
Planning - Planning involves determining what needs to be done.
Organizing: Organizing refers to deciding how things should work.
Directing - This refers to getting people follow instructions.
Controlling - Controlling means ensuring that people carry out tasks according to plan.
Six Sigma is so popular.
Six Sigma is easy to use and can lead to significant improvements. It can also be used to help companies identify and focus on the most important aspects of their business.
Statistics
- The BLS says that financial services jobs like banking are expected to grow 4% by 2030, about as fast as the national average. (wgu.edu)
- 100% of the courses are offered online, and no campus visits are required — a big time-saver for you. (online.uc.edu)
- UpCounsel accepts only the top 5 percent of lawyers on its site. (upcounsel.com)
- This field is expected to grow about 7% by 2028, a bit faster than the national average for job growth. (wgu.edu)
- Hire the top business lawyers and save up to 60% on legal fees (upcounsel.com)
External Links
How To
How can Lean Manufacturing be done?
Lean Manufacturing is a method to reduce waste and increase efficiency using structured methods. They were developed in Japan by Toyota Motor Corporation (in the 1980s). It was designed to produce high-quality products at lower prices while maintaining their quality. Lean manufacturing emphasizes removing unnecessary steps from the production process. It includes five main elements: pull systems (continuous improvement), continuous improvement (just-in-time), kaizen (5S), and continuous change (continuous changes). Pull systems involve producing only what the customer wants without any extra work. Continuous improvement is the continuous improvement of existing processes. Just-intime refers the time components and materials arrive at the exact place where they are needed. Kaizen refers to continuous improvement. It is achieved through small changes that are made continuously. Fifth, the 5S stand for sort, set up in order to shine, standardize, maintain, and standardize. These five elements are combined to give you the best possible results.
The Lean Production System
Six key concepts are the basis of lean production:
-
Flow - The focus is on moving information and material as close as possible to customers.
-
Value stream mapping: This is a way to break down each stage into separate tasks and create a flowchart for the entire process.
-
Five S’s - Sorted, In Order. Shine. Standardize. And Sustain.
-
Kanban - visual cues such as stickers or colored tape can be used to track inventory.
-
Theory of constraints - identify bottlenecks in the process and eliminate them using lean tools like kanban boards;
-
Just-intime - Order components and materials at your location right on the spot.
-
Continuous improvement - make incremental improvements to the process rather than overhauling it all at once.