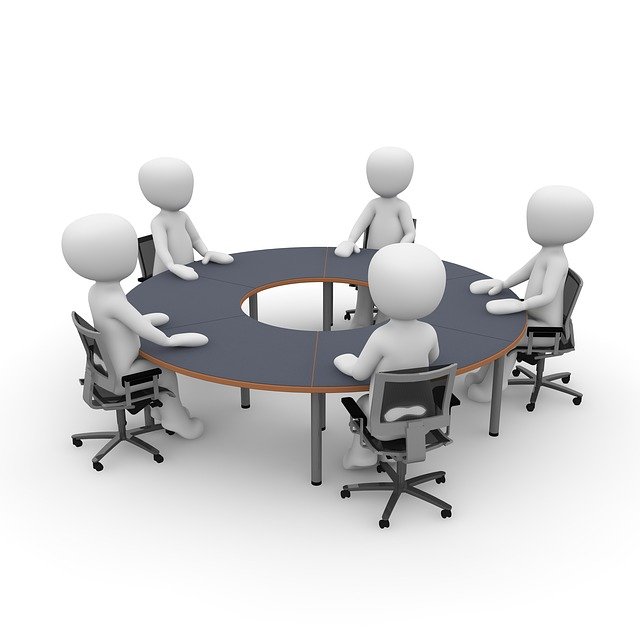
Although not required, being a certified construction manager does display your expertise. The Certified Construction Manager designation can be earned after passing a technical exam and gaining relevant experience. This designation is not cheap. As an applicant, you will need to take a self-study course on the professional role of a construction manager, risk allocation, and legal issues. The certification can be earned after passing an Associate Constructor exam and meeting other requirements.
Certificate
There are many types of certification available for construction managers. Associate Constructor Certification (AC), is the first, and it shows a high degree of construction manager skill. ACs must also adhere to the Code of Ethics of AIC. They are great for people with experience in another industry. This certification must also be renewed every three year. Certifications can be obtained either online or by passing exams.
A certificate in construction management is a great way to improve your skills and get a better salary. Employers will appreciate that you have the experience and knowledge to manage construction projects. Additionally, it differentiates small contractors from larger competitors by demonstrating that you can manage a project. However, the cost and type of training associated with obtaining a certificate varies. The Post-baccalaureate Certificate in Construction Management is for those who have completed a degree in construction. It can help you move up the ladder as a construction manager.
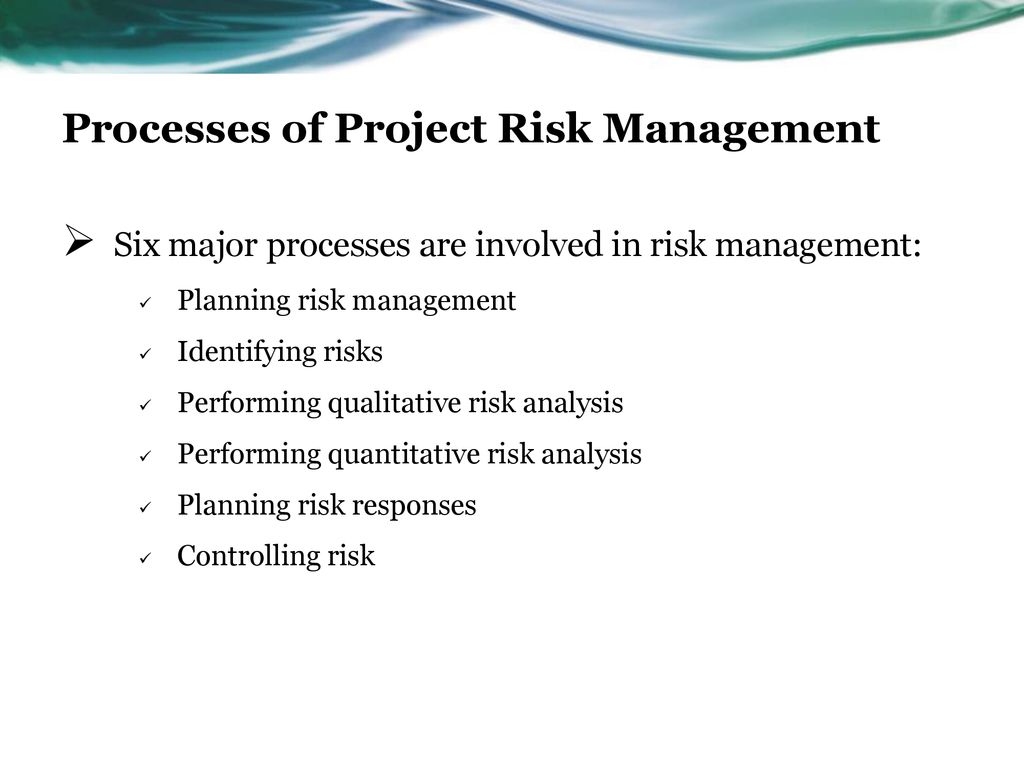
Education
You may be interested in pursuing a certificate of completion if you're seeking to further your education within the field. While it is not required to work, certification acts as a badge of distinction. It is proof of your commitment to the field and education. It also offers networking opportunities as the examining body will require proof of supervision hours before you can be awarded the certificate. The credentialing process can be boosted by professional organizations, which can assist you in your early career.
Students will learn the principles and practice of project management after completing the program. Students will gain knowledge about the project life cycle, including project management, general contracting, design-build, and more. It emphasizes the value of combining classroom learning and real-world experience. The program teaches students how to assess construction quality and the management process involved in each stage.
Experience
When preparing for a career in the construction industry, you should be aware of all the requirements for becoming a certified construction manager. An internship can be a good way to start your career, even if you don't have a degree from high school. While internships are often unpaid, they offer valuable experience in construction. Internships also give students the opportunity to be assistants to licensed construction managers. This can help them understand the responsibilities of their job.
The Certified Construction Manager (CCM credential) is the most prestigious in construction management. CCM certification, which is part of ISO 17024 is the only one to be accredited by ANSI, is the only one. Leading owner-consumers are increasingly specifying Certified Construction Managers in their construction RFPs. A growing number of organizations support the CCM designation with technical and financial support.
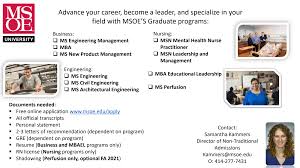
Salary
A salary for a qualified construction manager can vary. You may have different hazards depending on your work location. Higher risk jobs will lead to a higher salary and higher hazard pay. Managers who are certified workers may command a higher starting wage. Here are the best ways to get the most out your education and experience. A certified construction manager's salary can be as high as $75,000 or more per year.
Construction managers make a much higher salary than the national average. A construction manager can work with several consultants, including architects and civil engineers. Some projects require experts in structural steel, landscaping or painting, as well paving roads. They interact with lawyers, local government officials, and other professionals. A construction manager might also consult with city inspectors or a city planning official.
FAQ
What does "project management" mean?
This refers to managing all activities that are involved in a project's execution.
This includes defining the scope, identifying the requirements and preparing the budget. We also organize the project team, schedule the work, monitor progress, evaluate results, and close the project.
What can a manager do to improve his/her management skillset?
It is important to have good management skills.
Managers need to monitor their subordinates' performance.
You should immediately take action if you see that your subordinate is not performing as well as you would like.
You must be able to spot what is lacking and how you can improve it.
What is Six Sigma, exactly?
It's an approach to quality improvement that emphasizes customer service and continuous learning. It is a method that eliminates defects using statistical techniques.
Six Sigma was developed at Motorola in 1986 as part of its efforts to improve manufacturing processes.
The idea spread quickly throughout the industry, and today, many organizations are using six sigma methods to improve product design, production, delivery, and customer service.
Statistics
- Your choice in Step 5 may very likely be the same or similar to the alternative you placed at the top of your list at the end of Step 4. (umassd.edu)
- The profession is expected to grow 7% by 2028, a bit faster than the national average. (wgu.edu)
- Hire the top business lawyers and save up to 60% on legal fees (upcounsel.com)
- The average salary for financial advisors in 2021 is around $60,000 per year, with the top 10% of the profession making more than $111,000 per year. (wgu.edu)
- Our program is 100% engineered for your success. (online.uc.edu)
External Links
How To
How is Lean Manufacturing done?
Lean Manufacturing is a method to reduce waste and increase efficiency using structured methods. They were created by Toyota Motor Corporation in Japan in the 1980s. The aim was to produce better quality products at lower costs. Lean manufacturing is about eliminating redundant steps and activities from the manufacturing process. It has five components: continuous improvement and pull systems; just-in time; continuous change; and kaizen (continuous innovation). Pull systems allow customers to get exactly what they want without having to do extra work. Continuous improvement means continuously improving on existing processes. Just-in time refers to components and materials being delivered right at the place they are needed. Kaizen refers to continuous improvement. It is achieved through small changes that are made continuously. Last but not least, 5S is for sort. These five elements are used together to ensure the best possible results.
Lean Production System
Six key concepts make up the lean manufacturing system.
-
Flow is about moving material and information as near as customers can.
-
Value stream mapping: This is a way to break down each stage into separate tasks and create a flowchart for the entire process.
-
Five S's - Sort, Set In Order, Shine, Standardize, and Sustain;
-
Kanban - use visual signals such as colored tape, stickers, or other visual cues to keep track of inventory;
-
Theory of constraints - identify bottlenecks during the process and eliminate them with lean tools like Kanban boards.
-
Just-in time - Get components and materials delivered right at the point of usage;
-
Continuous improvement - incremental improvements are made to the process, not a complete overhaul.