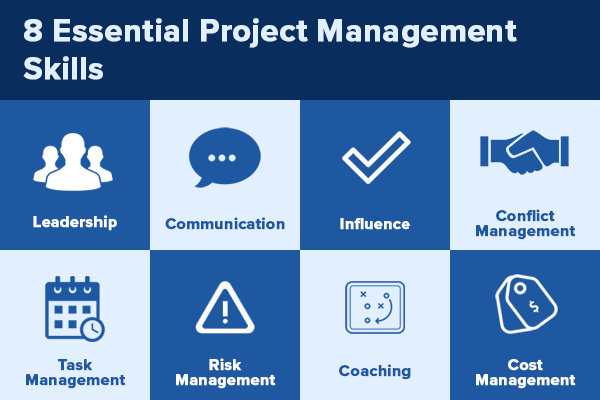
For those who want to progress in the field of construction management, accreditation is essential. Accreditation ensures that the college or university meets the standards for the profession it prepares its graduates. Learn more about the different accreditations available, including ABET ACCE and Louisiana State University.
ABET accreditation provides assurance that a college or university program meets the quality standards of the profession for which it prepares graduates
The ABET accreditation process guarantees that a college or university program meets the highest quality standards. It also prepares its graduates to succeed in their chosen profession. ABET's voluntary peer-review process adds value to technical programs and is highly regarded worldwide.
ABET's voluntary accreditation process is conducted by a team of volunteers representing government, industry, academe, and private practice. The team's focus is on the program's faculty and institutional support.
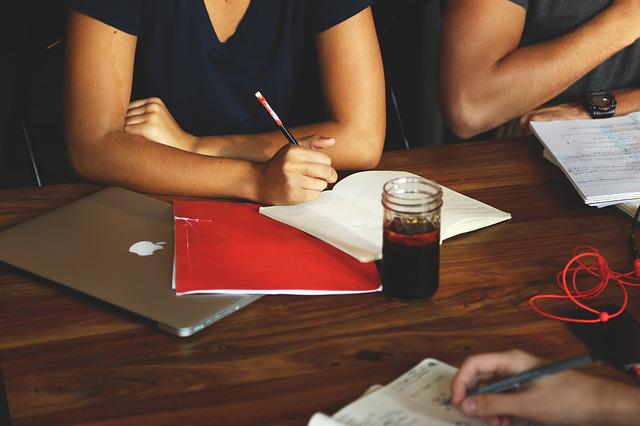
ACCE accreditation
ACCE accreditation is an asset for prospective students, employers, employees, and other stakeholders in the construction management field. Accredited programs give students the skills and knowledge needed to succeed in a career as a construction manager. Employers can find quality workers easier with accreditation. Accredited programs promote leadership development and foster networking.
American Council for Construction Education accredits both the Associate of Applied Science (ACCE) and the Bachelor of Science degrees in construction management. The Bachelor's program requires completion of a capstone course and internships within three years. Both programs require a minimum GPA of 3.0 and a minimum GRE score of 550. If applicants meet academic requirements, they may be permitted to transfer up to nine credits from other institutions. Accredited construction management education programs must maintain high quality standards and align their educational programs with industry requirements.
ABET accreditation
Accreditation by ABET for construction management programs is a great way of ensuring quality education and to make sure that program content is reviewed by an independent governing body. Accreditation Boards of Engineering and Technology (ABET), typically grant accreditation for programs in construction management. The ABET accreditation process demands that programs meet certain standards. Accredited programs are designed to prepare students for technical fields and keep them up-to-date on the latest technology.
Some schools may have multiple curricula, which are not all accredited with the same ABET. In such cases, the curriculum may contain core courses common to both programs. This may lead to student competition and overextension of resources.
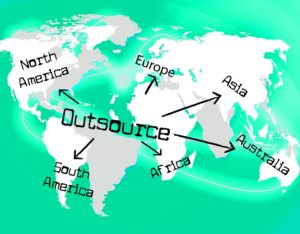
Louisiana State University accreditation
Louisiana State University's master's degree program in construction management gives you the skills and training required to manage a project. You'll learn all about construction design and delivery. Additionally, you will learn how to incorporate sustainable practices in the construction process. This program is approved by the American Council for Construction Education. The program includes leadership courses as well as core construction courses to help you become skilled construction managers.
Louisiana State University offers an Online Bachelor of Science Degree in Construction Management. This program consists of six CM courses, which will provide you with a fundamental knowledge base for the field. Once you have completed the requirements of the program, you will gain an unique perspective on this field.
FAQ
What can a manager do to improve his/her management skillset?
You can improve your management skills by practicing them at all times.
Managers must constantly monitor the performance of their subordinates.
You must act quickly if you notice that your subordinate isn’t performing to their standards.
You must be able to spot what is lacking and how you can improve it.
What are the steps of the management decision-making process?
The decision-making process of managers is complicated and multifaceted. It involves many factors, including but not limited to analysis, strategy, planning, implementation, measurement, evaluation, feedback, etc.
Management of people requires that you remember that they are just as human as you are, and can make mistakes. As such, there are always opportunities for improvement, especially when you put in the effort to improve yourself.
In this video, we explain what the decision-making process looks like in Management. We'll discuss the different types and reasons they are important. Managers should also know how to navigate them. These topics are covered in this course:
What are the five management steps?
The five stages of any business are planning, execution, monitoring, review, and evaluation.
Planning involves setting goals for the future. Planning includes setting goals for the future.
Execution happens when you actually do the plan. Everyone involved must follow them.
Monitoring is the act of monitoring your progress towards achieving your targets. Monitoring should include regular reviews of performance against goals and budgets.
At the end of every year, reviews take place. They provide an opportunity to assess whether everything went well during the year. If not there are changes that can be made to improve the performance next year.
Following the annual review, evaluation is done. It helps you identify the successes and failures. It also provides feedback on the performance of people.
What is Kaizen?
Kaizen is a Japanese term for "continuous improvement." It encourages employees constantly to look for ways that they can improve their work environment.
Kaizen is based upon the belief that each person should be capable of doing his or her job well.
What is a fundamental management tool for decision-making?
A decision matrix is a simple but powerful tool for helping managers make decisions. It helps them think systematically about all the options available to them.
A decision matrix represents alternatives in rows and columns. This allows you to easily see how each choice affects others.
This example shows four options, each represented by the boxes on either side of the matrix. Each box represents a different option. The top row depicts the current status quo, while the bottom row represents what would happen if no action was taken.
The effect of selecting Option 1 is shown in the middle column. It would increase sales by $2 million to 3 million in this instance.
The next two columns show the effects of choosing Options 2 and 3. These are both positive changes that increase sales by $1million and $500,000. However, these also involve negative consequences. Option 2 increases the cost of goods by $100,000. Option 3 decreases profits and makes them less attractive by $200,000.
Finally, the last column shows the results of choosing Option 4. This involves decreasing sales by $1 million.
The best thing about using a decision matrix is that you don't need to remember which numbers go where. It's easy to see the cells and instantly know if any one of them is better than another.
This is because the matrix has done all the hard work. It's simply a matter of comparing the numbers in the relevant cells.
Here's an example of how you might use a decision matrix in your business.
You need to decide whether to invest in advertising. You'll be able increase your monthly revenue by $5000 if you do. But, you will also incur additional expenses of $10 thousand per month.
By looking at the cell just below "Advertising", the net result can be calculated as $15 thousand. Advertising is worth much more than the investment cost.
What are some common mistakes managers make?
Managers sometimes make their own job harder than necessary.
They may not delegate enough responsibilities and not provide sufficient support.
In addition, many managers lack the communication skills required to motivate and lead their teams.
Some managers set unrealistic expectations for their staff.
Managers might try to solve every problem by themselves rather than delegating the responsibility.
How can a manager motivate employees?
Motivation refers to the desire to perform well.
It is possible to be motivated by doing something you enjoy.
You can also feel motivated by making a positive contribution to the success in the organization.
You might find it more rewarding to treat patients than to study medical books if you plan to become a doctor.
Another type of motivation comes from within.
One example is a strong sense that you are responsible for helping others.
Perhaps you enjoy working hard.
If you feel unmotivated, ask yourself why.
You can then think of ways to improve your motivation.
Statistics
- As of 2020, personal bankers or tellers make an average of $32,620 per year, according to the BLS. (wgu.edu)
- Hire the top business lawyers and save up to 60% on legal fees (upcounsel.com)
- UpCounsel accepts only the top 5 percent of lawyers on its site. (upcounsel.com)
- This field is expected to grow about 7% by 2028, a bit faster than the national average for job growth. (wgu.edu)
- Your choice in Step 5 may very likely be the same or similar to the alternative you placed at the top of your list at the end of Step 4. (umassd.edu)
External Links
How To
How does Lean Manufacturing work?
Lean Manufacturing uses structured methods to reduce waste, increase efficiency and reduce waste. These processes were created by Toyota Motor Corporation, Japan in the 1980s. The aim was to produce better quality products at lower costs. Lean manufacturing emphasizes removing unnecessary steps from the production process. It has five components: continuous improvement and pull systems; just-in time; continuous change; and kaizen (continuous innovation). The production of only what the customer needs without extra work is called pull systems. Continuous improvement is constantly improving upon existing processes. Just-in–time refers when components or materials are delivered immediately to their intended destination. Kaizen refers to continuous improvement. It is achieved through small changes that are made continuously. Five-S stands for sort. It is also the acronym for shine, standardize (standardize), and sustain. These five elements can be combined to achieve the best possible results.
Lean Production System
Six key concepts form the foundation of the lean production system:
-
Flow - focus on moving material and information as close to customers as possible;
-
Value stream mapping- This allows you to break down each step of a process and create a flowchart detailing the entire process.
-
Five S's – Sort, Put In Order Shine, Standardize and Sustain
-
Kanban - use visual signals such as colored tape, stickers, or other visual cues to keep track of inventory;
-
Theory of Constraints - Identify bottlenecks in the process, and eliminate them using lean tools such kanban boards.
-
Just-in-time delivery - Deliver components and materials right to your point of use.
-
Continuous improvement - Make incremental improvements rather than overhauling the entire process.