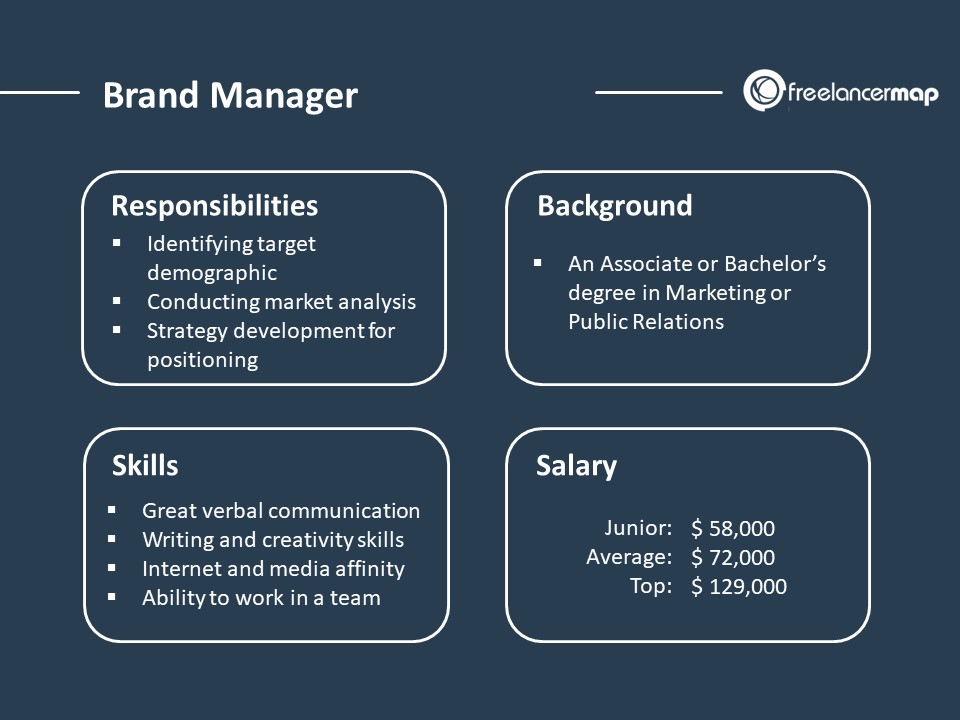
Negative return
Negative return or downside risk can be used to describe the exact same thing. They basically mean that an investment won't make money within a given time period. Exumor Chanels Inc. might lose 6% if it falls apart.
The study, which is based on high-frequency data and shows that negative return effects are more severe in emerging markets then in developed ones. However, this doesn't mean that downside risk is less of a concern in all markets. The study suggests that downside risks and negative returns are more prevalent in emerging markets. Therefore, it is important to evaluate negative return expectations and downside risk expectations before making any investment.
Loss of capital
A downside is a financial risk when you invest in a security which may lose its worth. This risk could be infinite or finite. Roy studied it first in 1952. He developed his theory to calculate the risk of securities losing. When deciding whether to buy a security, you should consider its potential downside risk.
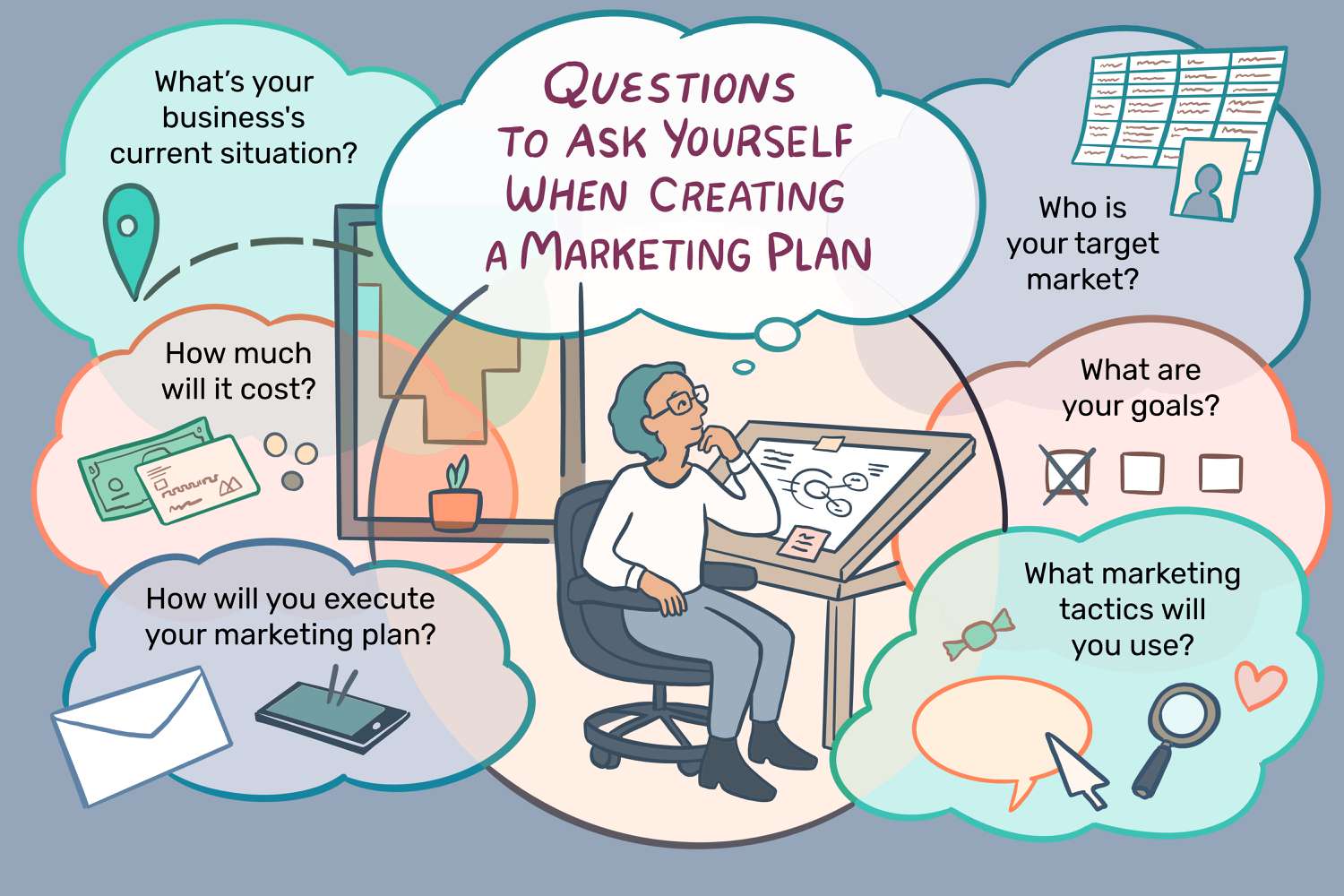
There are many ways to manage a downside risk. Among them are diversification, tactical asset allocation, and the use of derivative instruments. These strategies should be tailored to an investor's risk tolerance and time horizon. These strategies should be compatible with the associated costs.
Inflation
Inflation may drop for the first and only time in more than a decade. This is due to the fact that the Federal Reserve isn't expected to raise rates as frequently as market expectations. The Fed has not raised interest rates this year and has communicated about future increases. This has already led to mortgage rates and Treasury yields rising. The Fed is expected to raise interest rates gradually, which will help keep inflation under control.
Inflation has the potential to depress consumer spending. This is a serious risk that could impact economic growth. Consumers may have less money to spend fun items if their everyday staples cost rise. This could result in a slowdown of the economy, which could also affect the stock markets.
Volatility
Investing is a complex business. You need to understand volatility and downside risk. When one invests, it is important to minimize the downside risks while simultaneously maximising the upside. The volatility of the markets is basically a measure how high the risk of a security. This is sometimes referred to simply as "the risk losing money". Volatility refers to the degree of risk that an investment has before it is fully realised.
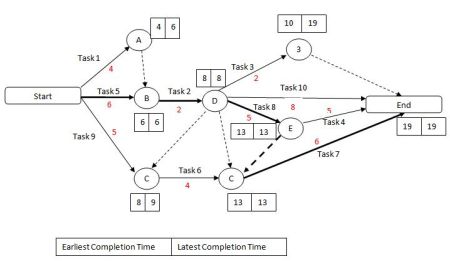
Investors may lose money if the investment's value goes down. This is called the downside risk. There are many ways to calculate this risk. The easiest method is to compare the upside and downside potential of a security. Positive potential is the possibility that security's value will increase in the future.
Liquidity
Two types of trading risks should be considered. One type is market liquidity risk. This is due to withdrawals from markets. Another type of risk is the downside risk. The price of an asset may drop to zero, but it might also go up above the listing price when the market recovers. These risks could negatively impact your profits or losses.
Funding liquidity risk is a risk that a firm may not be able to meet its future cash flow requirements, or its current cash needs. This risk can adversely affect a firm's ability to operate. This is especially true for financial institutions. One of the ways to address this risk is by implementing debt maturity transformation.
FAQ
How can we create a culture of success in our company?
A successful company culture is one that makes people feel valued and respected.
It is founded on three basic principles:
-
Everybody can contribute something valuable
-
Fair treatment of people is the goal
-
There is mutual respect between individuals and groups
These values are reflected by the way people behave. They will treat others with respect and kindness.
They will be respectful of the opinions of other people.
These people will inspire others to share thoughts and feelings.
The company culture promotes collaboration and open communication.
People feel comfortable expressing their opinions freely without fear of reprisal.
They know that they will not be judged if they make mistakes, as long as the matter is dealt with honestly.
Finally, the company culture encourages honesty as well as integrity.
Everyone knows that they must always tell the truth.
Everyone is aware that rules and regulations apply to them.
Nobody expects to be treated differently or given favors.
How does Six Sigma function?
Six Sigma uses statistical analysis to find problems, measure them, analyze root causes, correct problems, and learn from experience.
First, identify the problem.
Next, data are collected and analyzed in order to identify patterns and trends.
The problem can then be fixed by taking corrective measures.
The data are then reanalyzed to see if the problem is solved.
This cycle continues until there is a solution.
What is the main difference between Six Sigma Six Sigma TQM and Six Sigma Six Sigma?
The key difference between the two quality management tools is that while six-sigma focuses its efforts on eliminating defects, total quality management (TQM), focuses more on improving processes and reducing cost.
Six Sigma is a method for continuous improvement. This method emphasizes eliminating defects using statistical methods such p-charts, control charts, and Pareto analysis.
The goal of this method is to reduce variation in product output. This is done by identifying and correcting the root causes of problems.
Total Quality Management involves monitoring and measuring every aspect of the organization. It also involves training employees to improve performance.
It is often used as a strategy to increase productivity.
Statistics
- The BLS says that financial services jobs like banking are expected to grow 4% by 2030, about as fast as the national average. (wgu.edu)
- The average salary for financial advisors in 2021 is around $60,000 per year, with the top 10% of the profession making more than $111,000 per year. (wgu.edu)
- As of 2020, personal bankers or tellers make an average of $32,620 per year, according to the BLS. (wgu.edu)
- Hire the top business lawyers and save up to 60% on legal fees (upcounsel.com)
- Our program is 100% engineered for your success. (online.uc.edu)
External Links
How To
What is Lean Manufacturing?
Lean Manufacturing methods are used to reduce waste through structured processes. They were created in Japan by Toyota Motor Corporation during the 1980s. It was designed to produce high-quality products at lower prices while maintaining their quality. Lean manufacturing emphasizes removing unnecessary steps from the production process. It includes five main elements: pull systems (continuous improvement), continuous improvement (just-in-time), kaizen (5S), and continuous change (continuous changes). Pull systems involve producing only what the customer wants without any extra work. Continuous improvement involves constantly improving upon existing processes. Just-in–time refers when components or materials are delivered immediately to their intended destination. Kaizen means continuous improvement, which is achieved by implementing small changes continuously. Last but not least, 5S is for sort. These five elements are combined to give you the best possible results.
Lean Production System
Six key concepts underlie the lean production system.
-
Flow - The focus is on moving information and material as close as possible to customers.
-
Value stream mapping: This is a way to break down each stage into separate tasks and create a flowchart for the entire process.
-
Five S's, Sort, Set in Order, Shine. Standardize. and Sustain.
-
Kanban: Use visual signals such stickers, colored tape, or any other visual cues, to keep track your inventory.
-
Theory of Constraints - Identify bottlenecks in the process, and eliminate them using lean tools such kanban boards.
-
Just-intime - Order components and materials at your location right on the spot.
-
Continuous improvement - make incremental improvements to the process rather than overhauling it all at once.