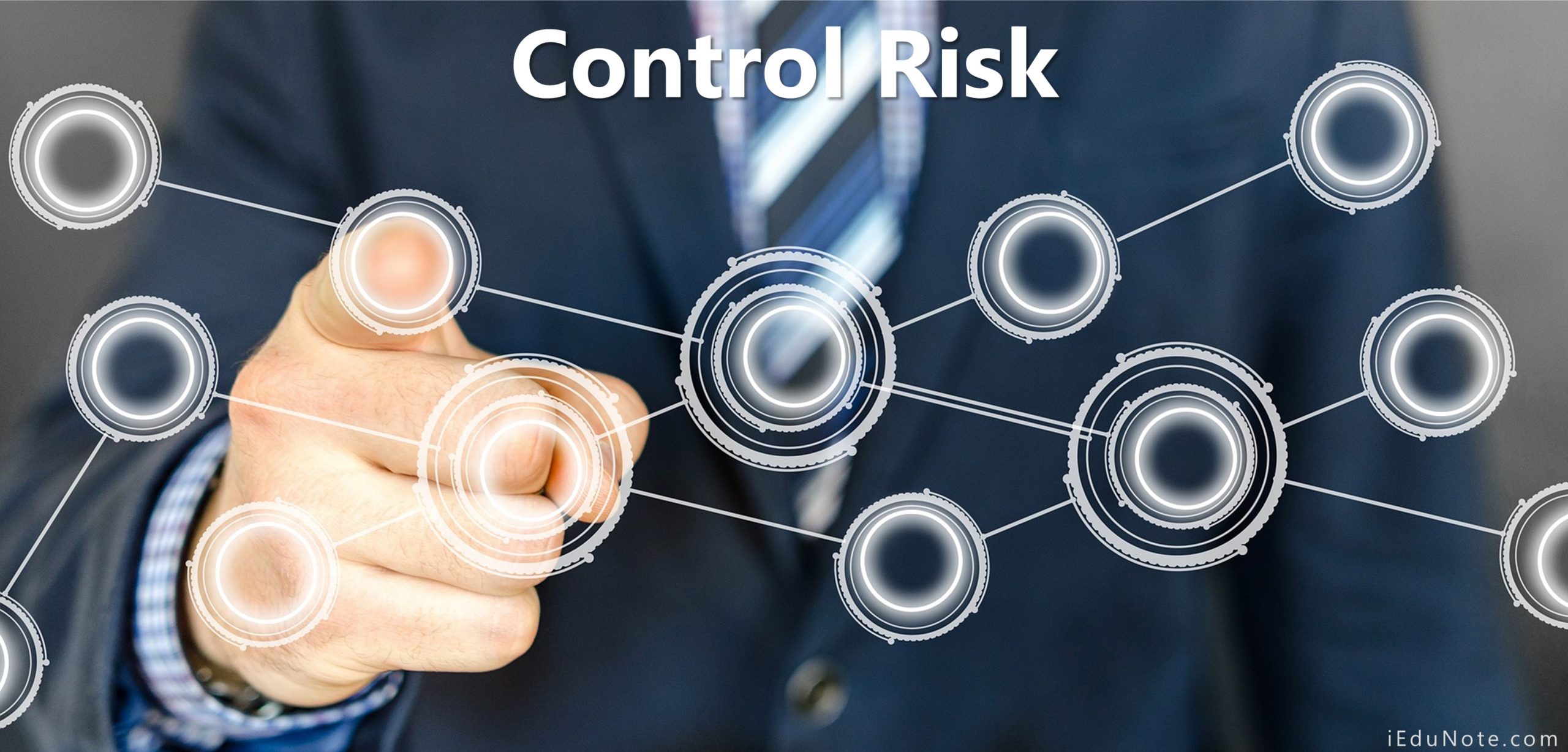
The Waste Management Specialist will be responsible for creating project schedules, and making service recommendations. In partnership with the National Account Manager, this position develops client relationships and new program initiatives. The Waste Management Specialist is a part of the team and helps associates achieve professional standards. They also actively participate in professional development. They also coordinate with the National Account Manager to ensure that clients are getting the best possible service from the company. In addition, this position oversees projects and leads project teams.
Jim Bentley
Advanced Disposal National Accounts and the commercial arm of the company are both waste management companies. Jim Bentley will develop relationships with potential clients, clients, and strategic partner vendors. He will also lead business development for other companies in the company’s vast network that includes over 7,000 environmental service provider across North America. Bentley has more than 21 years experience in solid waste management, most recently working as a senior executive for Green Leaf Compaction.
Ashish Sharma
Ashish Sharma, the senior manager of digital for Waste Management leads the technology and solutions teams in the company’s Asset Management division. He is also responsible for the digital team involved in New York's Marine Transfer Station. He joined Waste Management in 2014. Previously, he held senior leadership positions in IBM and Deloitte & Touche, LLC. He has more 16 years experience in the technology sector.
Sharma has managed many different projects in his time at Waste Management. Recent experience includes working on New York’s marine transfer stations, which was part of Waste Management's $3.3billion contract with Sanitation. Sharma was also honored with the Waste360 40 Under 40 award. This recognition highlights his leadership and innovation in waste management. Ashish Sharma has won a number of industry awards, including the prestigious "Best New Product" award from Waste360.
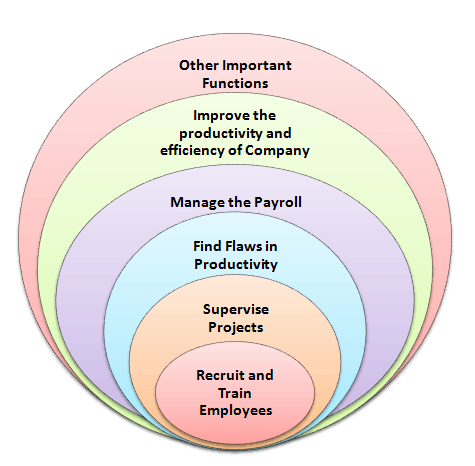
FAQ
What are the key management skills?
No matter if they are running a local business or an international one, management skills are vital. These skills include the ability manage people, finances and resources as well as other factors.
These skills are necessary for setting goals and objectives as well as planning strategies, leading groups, motivating employees and solving problems.
As you can see, there's no end to the list of managerial duties!
What are the five management steps?
Each business has five stages: planning, execution and monitoring.
Planning involves setting goals for the future. It includes defining what you want to achieve and how you plan to do it.
Execution takes place when you actually implement the plans. These plans must be adhered to by everyone.
Monitoring is the process of evaluating your progress toward achieving your objectives. Monitoring should include regular reviews of performance against goals and budgets.
Review events take place at each year's end. They allow for an assessment of whether all went well throughout the year. If not, it is possible to make improvements for next year.
After the annual review is complete, evaluations are conducted. It helps to identify what went well and what didn’t. It provides feedback about how people perform.
What are the 4 main functions of management?
Management is responsible in planning, organizing and directing people and resources. This includes setting goals, developing policies and procedures, and creating procedures.
Management aids an organization in reaching its goals by providing direction and coordination, control, leadership motivation, supervision, training, evaluation, and leadership.
Management's four main functions are:
Planning - Planning is about determining what must be done.
Organizing is the act of deciding how things should go.
Directing - This refers to getting people follow instructions.
Controlling - Controlling means ensuring that people carry out tasks according to plan.
Statistics
- The BLS says that financial services jobs like banking are expected to grow 4% by 2030, about as fast as the national average. (wgu.edu)
- The profession is expected to grow 7% by 2028, a bit faster than the national average. (wgu.edu)
- UpCounsel accepts only the top 5 percent of lawyers on its site. (upcounsel.com)
- 100% of the courses are offered online, and no campus visits are required — a big time-saver for you. (online.uc.edu)
- As of 2020, personal bankers or tellers make an average of $32,620 per year, according to the BLS. (wgu.edu)
External Links
How To
What is Lean Manufacturing?
Lean Manufacturing techniques are used to reduce waste while increasing efficiency by using structured methods. They were developed in Japan by Toyota Motor Corporation (in the 1980s). The primary goal was to make products with lower costs and maintain high quality. Lean manufacturing focuses on eliminating unnecessary steps and activities from the production process. It includes five main elements: pull systems (continuous improvement), continuous improvement (just-in-time), kaizen (5S), and continuous change (continuous changes). It is a system that produces only the product the customer requests without additional work. Continuous improvement involves constantly improving upon existing processes. Just-in-time refers to when components and materials are delivered directly to the point where they are needed. Kaizen refers to continuous improvement. It is achieved through small changes that are made continuously. Finally, 5S stands for sort, set in order, shine, standardize, and sustain. These five elements can be combined to achieve the best possible results.
Lean Production System
The lean production system is based on six key concepts:
-
Flow - focuses on moving information and materials as close to customers as possible.
-
Value stream mapping- This allows you to break down each step of a process and create a flowchart detailing the entire process.
-
Five S's: Sort, Shine Standardize, Sustain, Set In Order, Shine and Shine
-
Kanban - use visual signals such as colored tape, stickers, or other visual cues to keep track of inventory;
-
Theory of Constraints - Identify bottlenecks in the process, and eliminate them using lean tools such kanban boards.
-
Just-in-time - deliver components and materials directly to the point of use;
-
Continuous improvement: Make incremental improvements to the process instead of overhauling it completely.